Subsea Interconnectors: The Giants Beneath the Waves
Picture a giant steel serpent. These aren’t mythical sea creatures—they’re subsea interconnectors!
These invisible arteries, comprising high-voltage cables laid beneath the sea, enable electricity to flow seamlessly between countries.
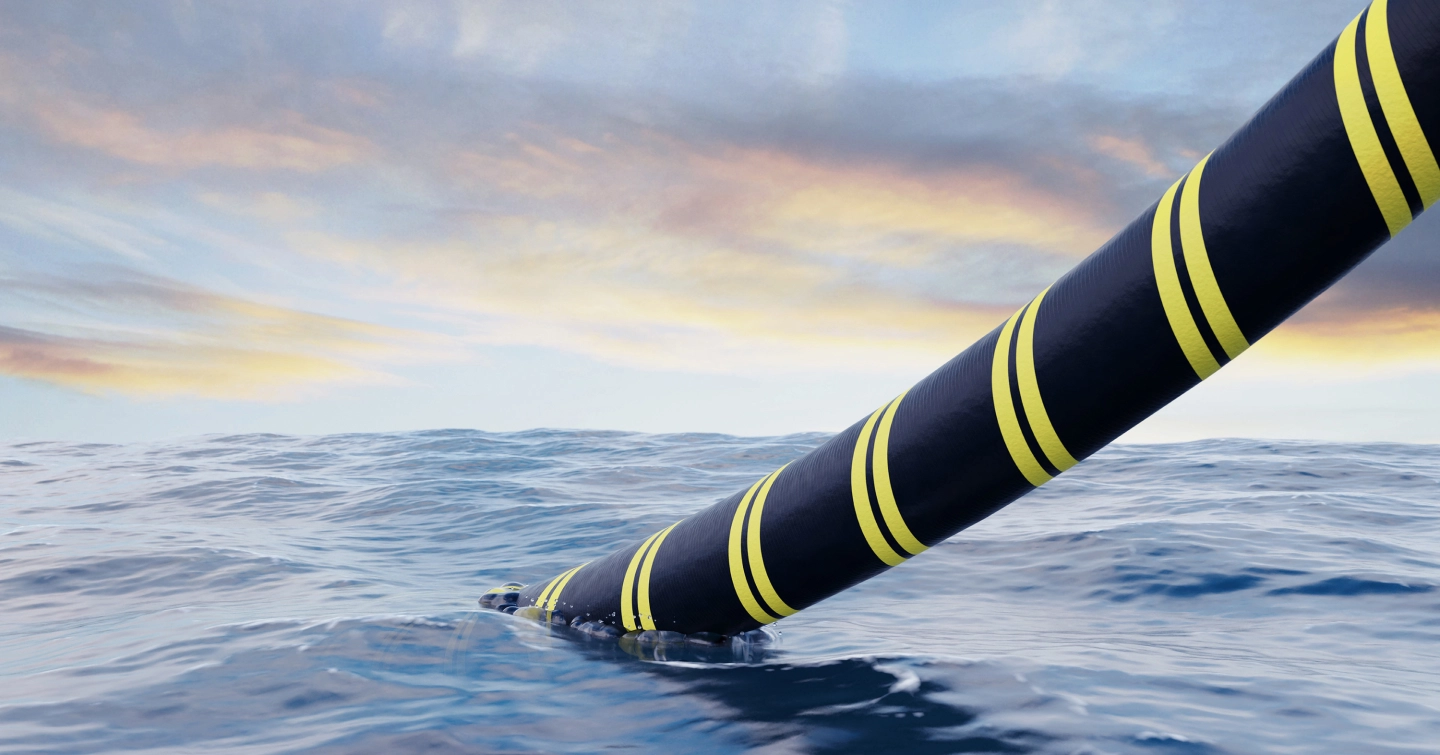
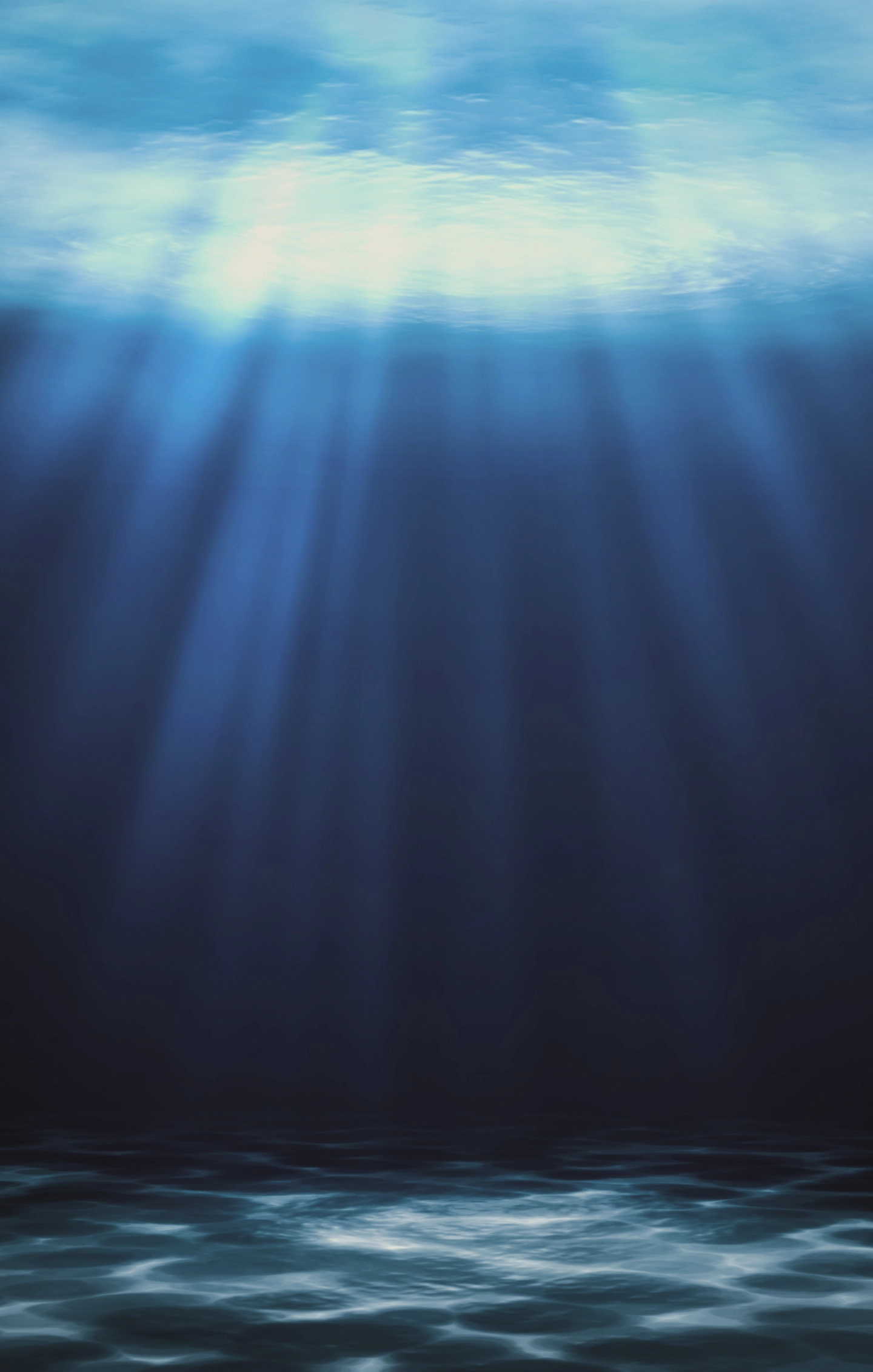
Diameter
Up to 300 mm
The girth of these marine giants
Weight
200 kg
Each meter can weigh up to 200 kg
Maximum Depth
3 000 m
Currently reaching
installation depths of 3,000 m (as of 2025)
Europe,
The Most
Connected Continent
Key Projects
Great Sea Interconnector (2028)
Crete to Cyprus
2×900 km HVDC cables,
the largest interconnection project in history
Facilitating energy exchange, integrating renewables, and powering 3 million homes.
Celtic Interconnector (2026)
France to Ireland
2×500 km HVDC cables, the longest in the world
Linking Ireland to mainland Europe for the first time, with a 700 MW capacity—enough to power 450,000 homes—while enhancing Ireland’s energy security.
Crete-Attica Interconnector
Crete to mainland Greece
335 km HVDC cable at 1,200 meters depth
Ensures Crete’s energy supply while transitioning from fossil fuels to wind and solar power.
NordLink Interconnector
Germany to Norway
2×700 km subsea cables with a 1,400 MW capacity
Enables the exchange and storage of renewable energy between Norway and Germany.
Europe, The Most Connected Continent
Europe leads the way in interconnection technology, boasting an exceptionally sophisticated network that relies heavily on subsea cables.
Key Projects
Great Sea Interconnector (2028)
Crete to Cyprus
2×900 km HVDC cables, the largest interconnection project in history,
Facilitating energy exchange, integrating renewables, and powering 3 million homes.
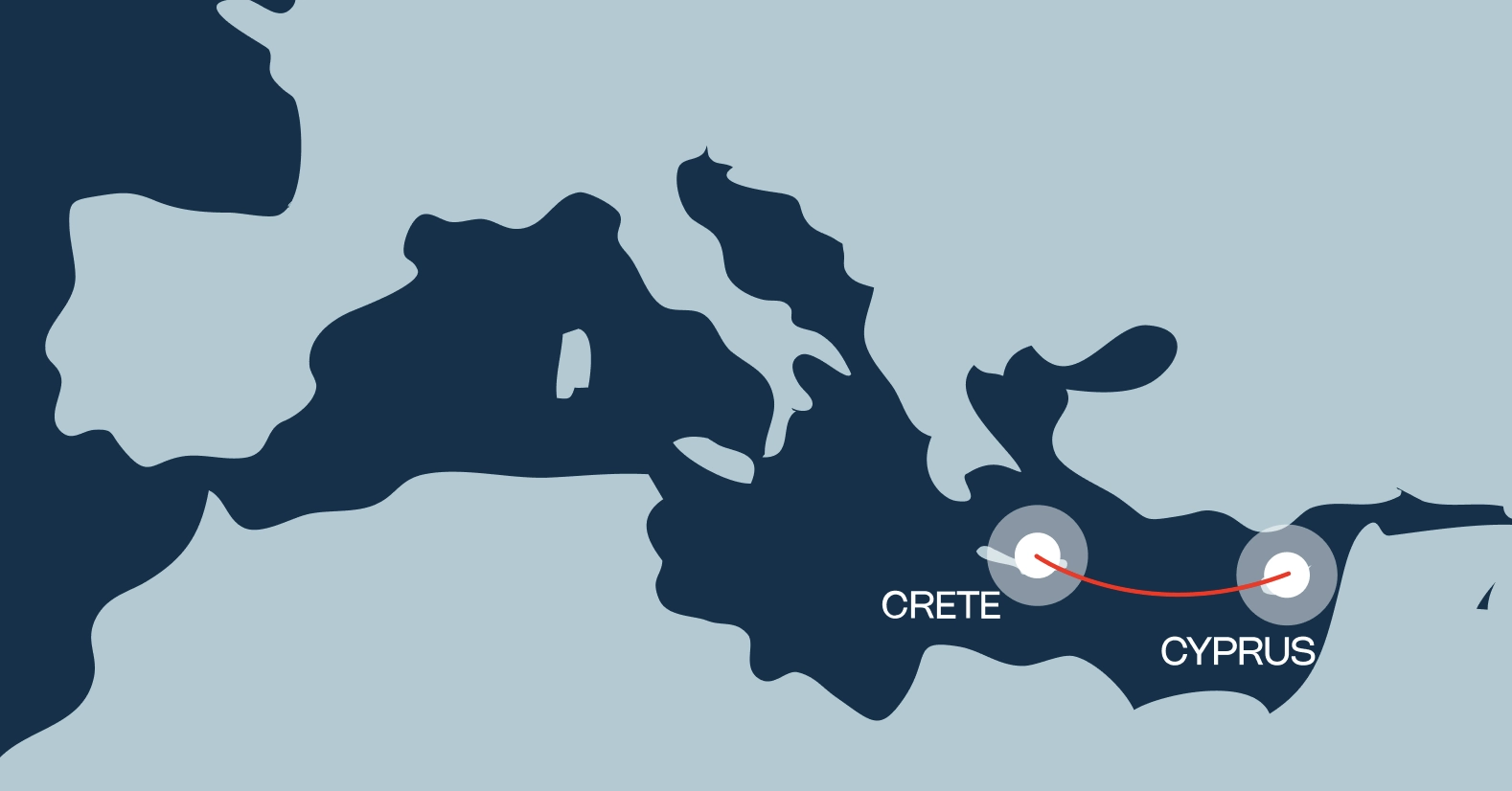
Key Projects
Celtic Interconnector (2026)
France to Ireland
2×500 km HVDC cables, the longest in the world
Linking Ireland to mainland Europe for the first time, with a 700 MW capacity—enough to power 450,000 homes—while enhancing Ireland’s energy security.
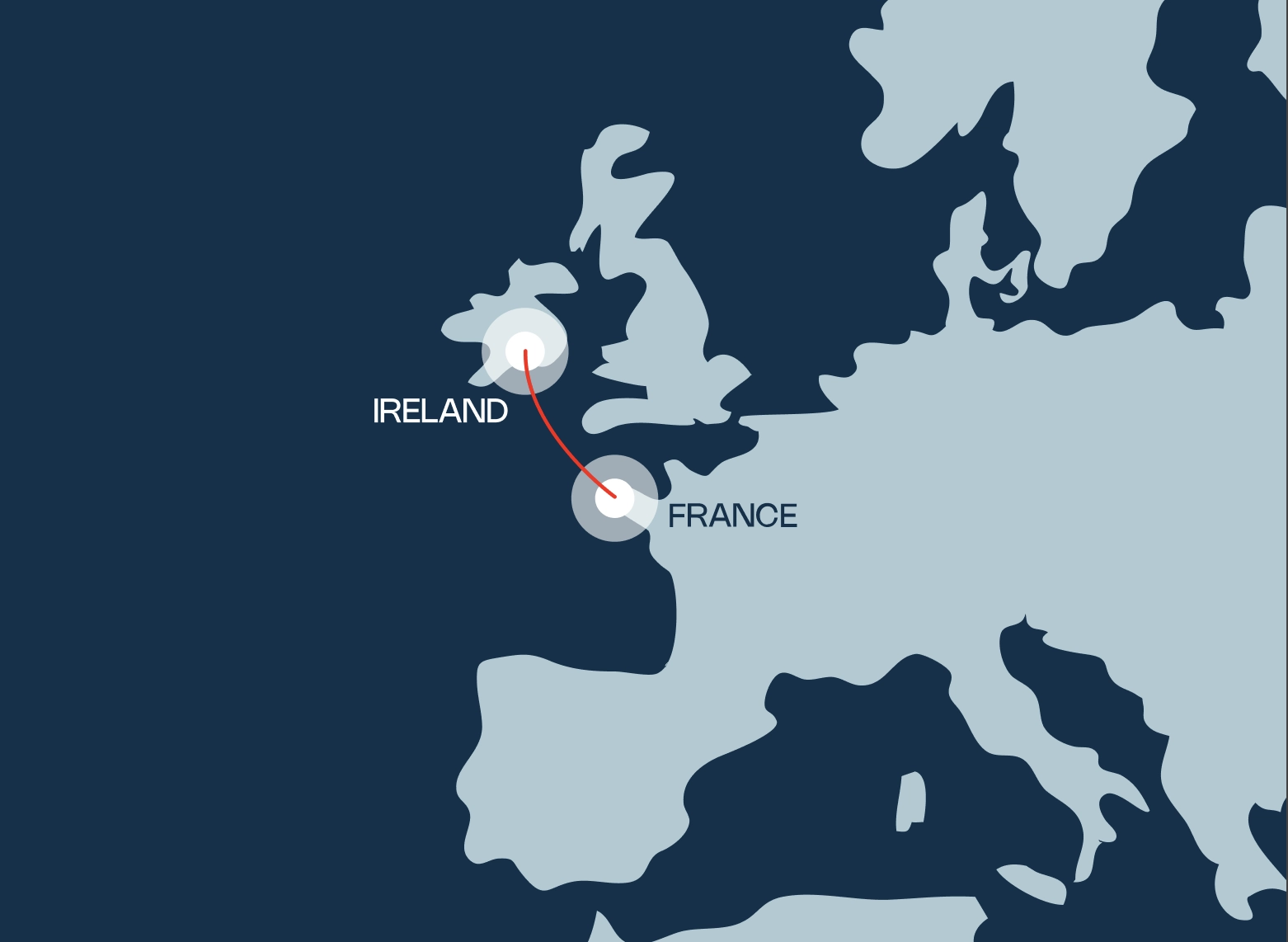
Key Projects
Crete-Attica Interconnector
Crete to mainland Greece
335 km HVDC cable at 1,200 meters depth
Ensures Crete’s energy supply while transitioning from fossil fuels to wind and solar power.
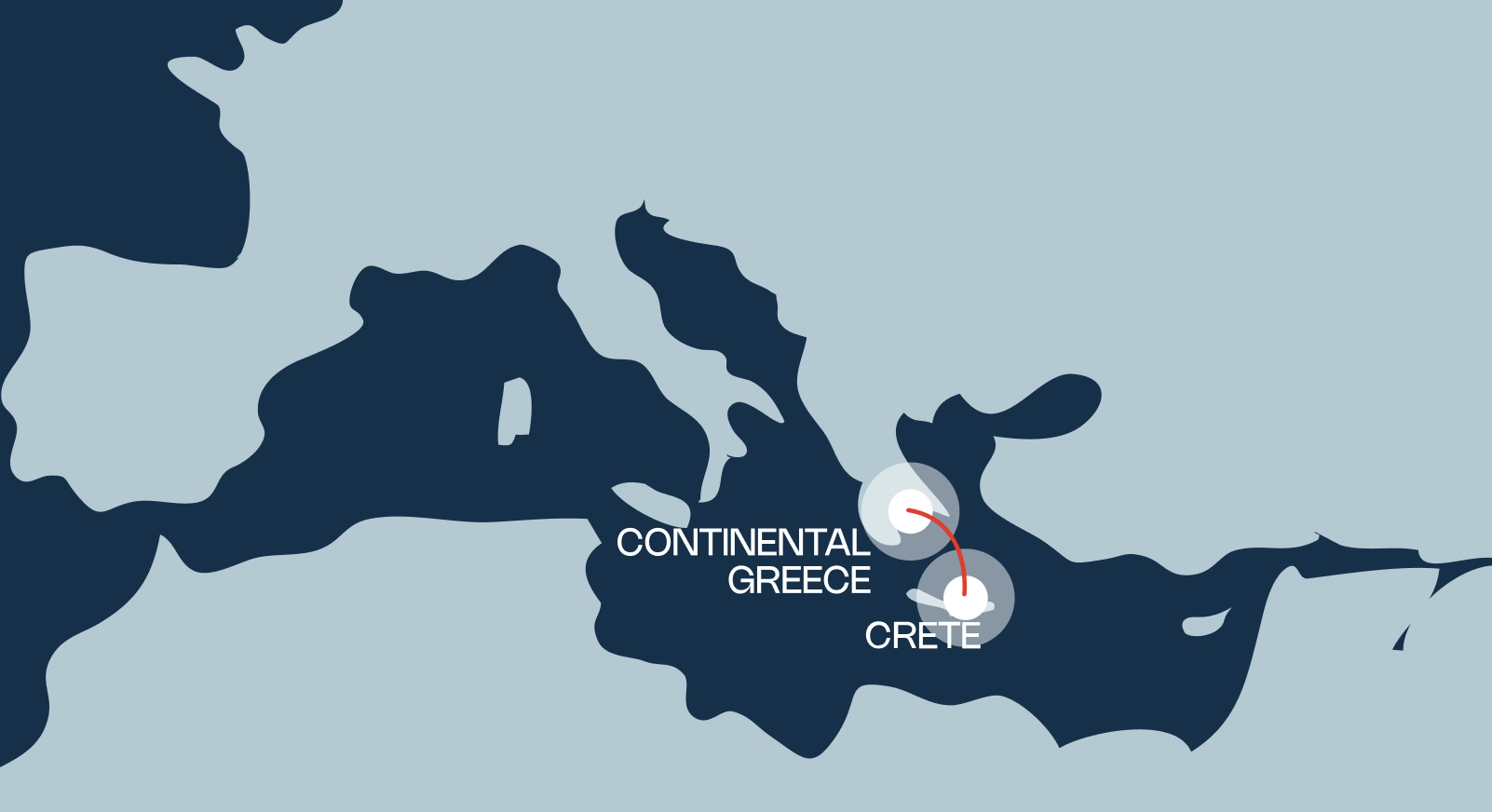
Key Projects
NordLink Interconnector
Germany to Norway
2×700 km subsea cables with a 1,400 MW capacity
Enables the exchange and storage of renewable energy between Norway and Germany.
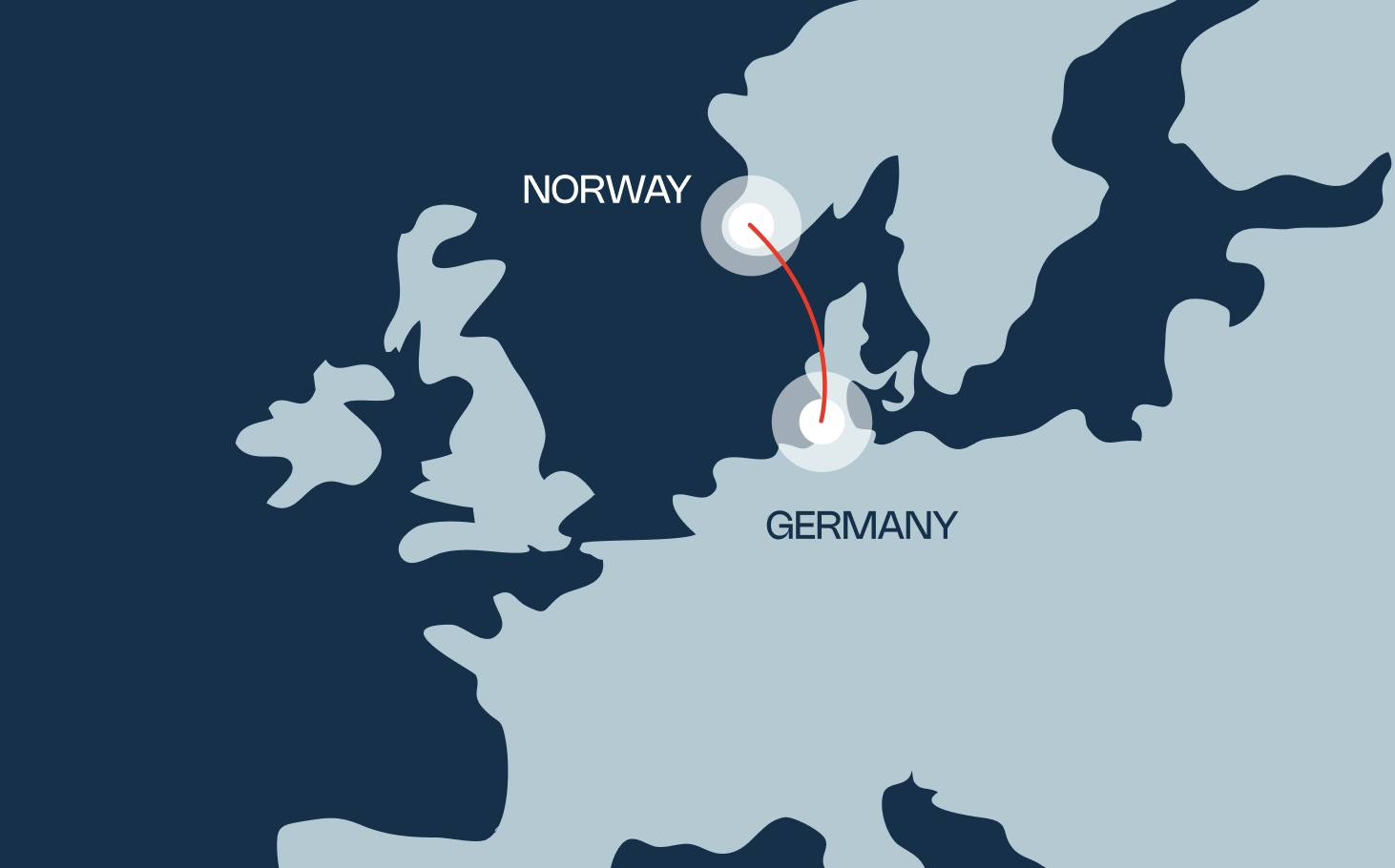
Why Subsea Interconnections Matter
Securing and Balancing Grids
By linking power grids, energy can be redistributed where needed. Solar energy from Morocco can power Northern Europe, while Norway’s hydroelectricity can flow south.
This system enhances resilience by balancing surpluses and deficits.
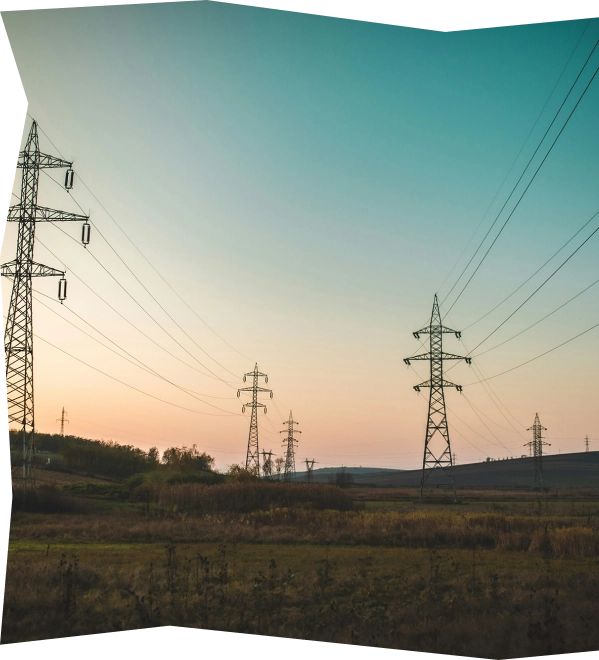
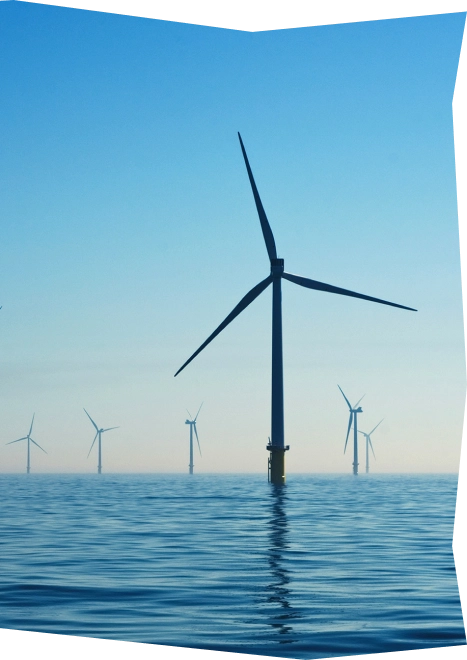
Amplifying Renewable Energy Use
Excess renewable energy, instead of being wasted, can be transferred to regions with high demand.
Maximizing Socioeconomic Benefits
Enhanced interconnections translate to significant consumer savings through a more efficient energy network.
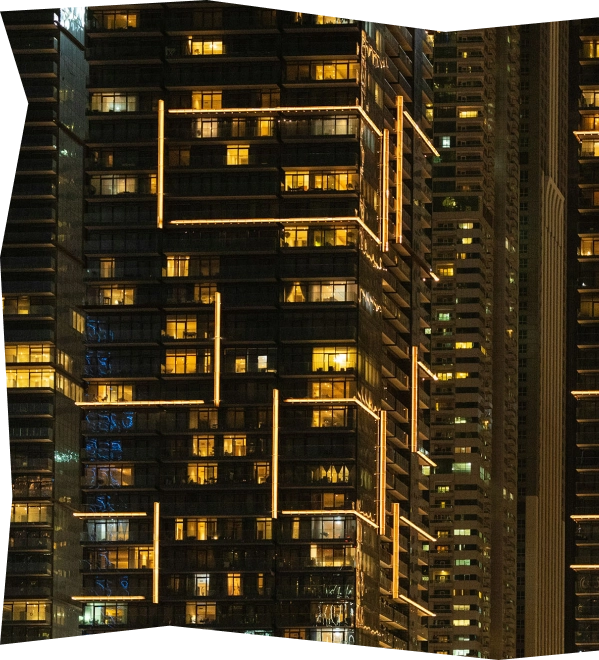
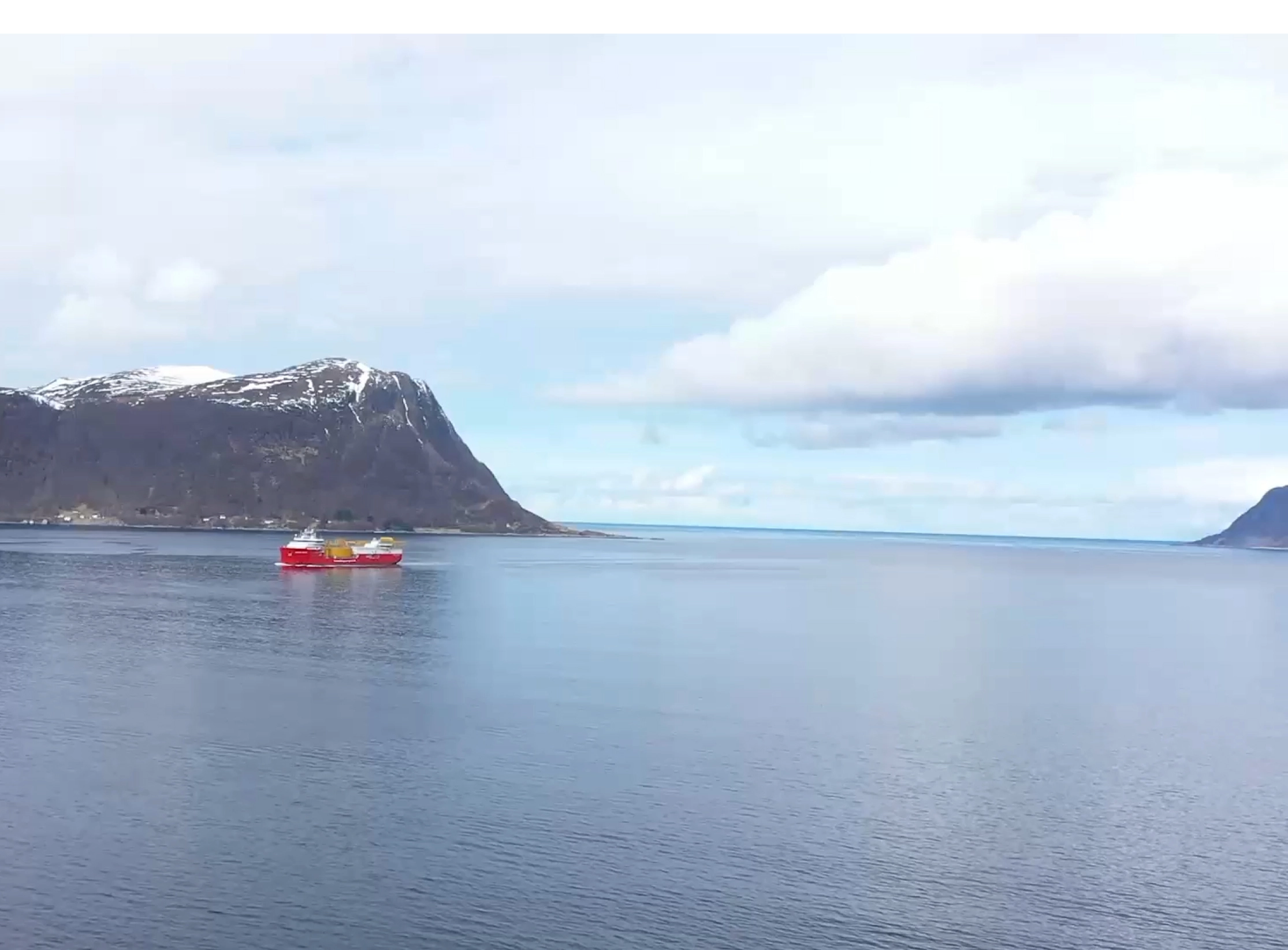
The Nexans Fleet:
At the Forefront
Cable-laying vessels (CLVs) are integral to the subsea interconnection process.
These technological marvels, some exceeding 100 meters in length, transport and deploy the cables with precision.
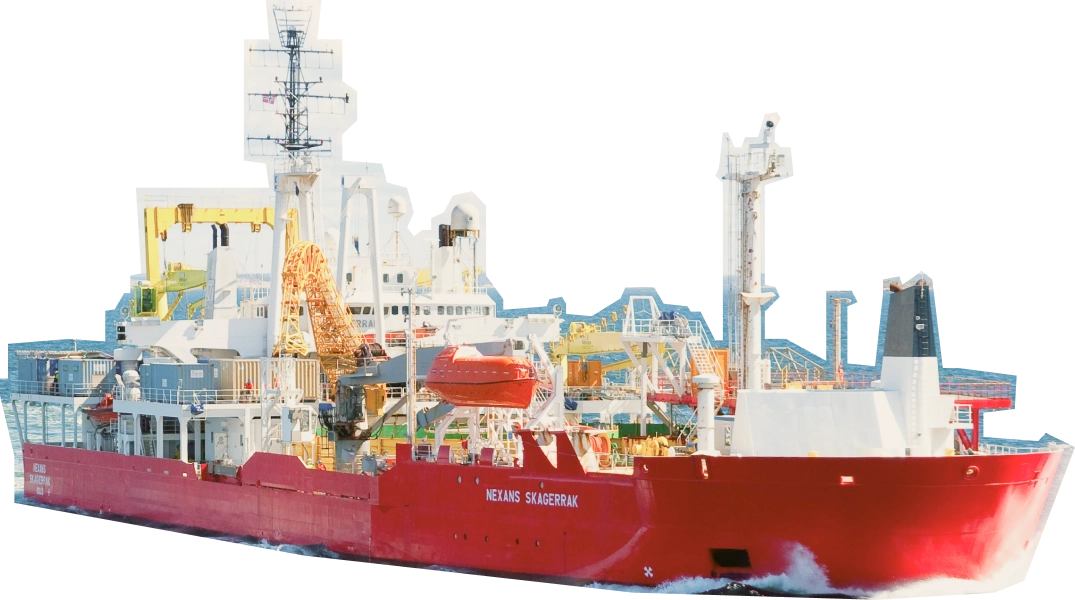
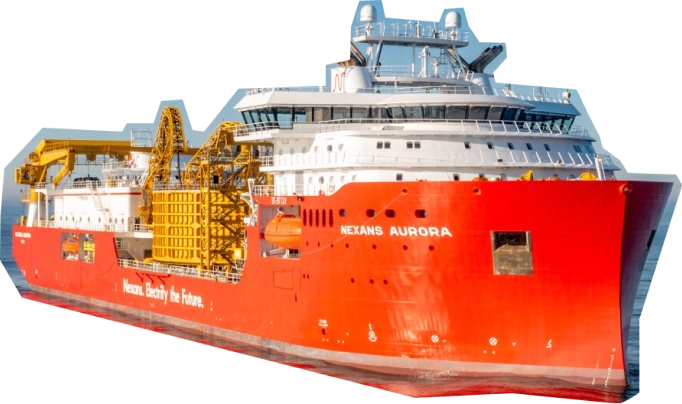
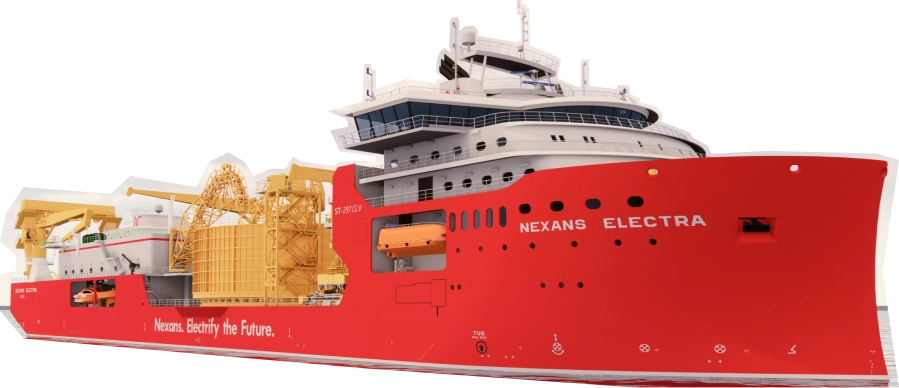
C/S Nexans Skagerrak
Size
118.5 m long, 32.15 m wide
Speciality
Safe and efficient transport of HVAC and HVDC cable systems.
Size
149.9 m long, 31 m wide
Speciality
Handles up to 10,000 tons of cable (equivalent to the Eiffel Tower’s weight) and performs high-voltage installations.
Size
149.9 m long, 31 m wide
Speciality
Simultaneous laying of four cables, with a load capacity of 13,500 tons and state-of-the-art robotic systems for burial and jetting.
Subsea interconnections are transforming global power grids by enabling secure and efficient electricity exchanges between nations.
These colossal cables, installed at incredible depths, support renewable energy integration by directing surplus production to areas with high demand.
Find out more
Subsea interconnections for borderless electricity
Renewable energy
23 / 07 / 2024
Immerse yourself in the world of submarine cables and discover how innovative technologies are transforming the way we transmit renewable energy. Learn more about the sustainable solutions essential to powering our future efficiently and responsibly.
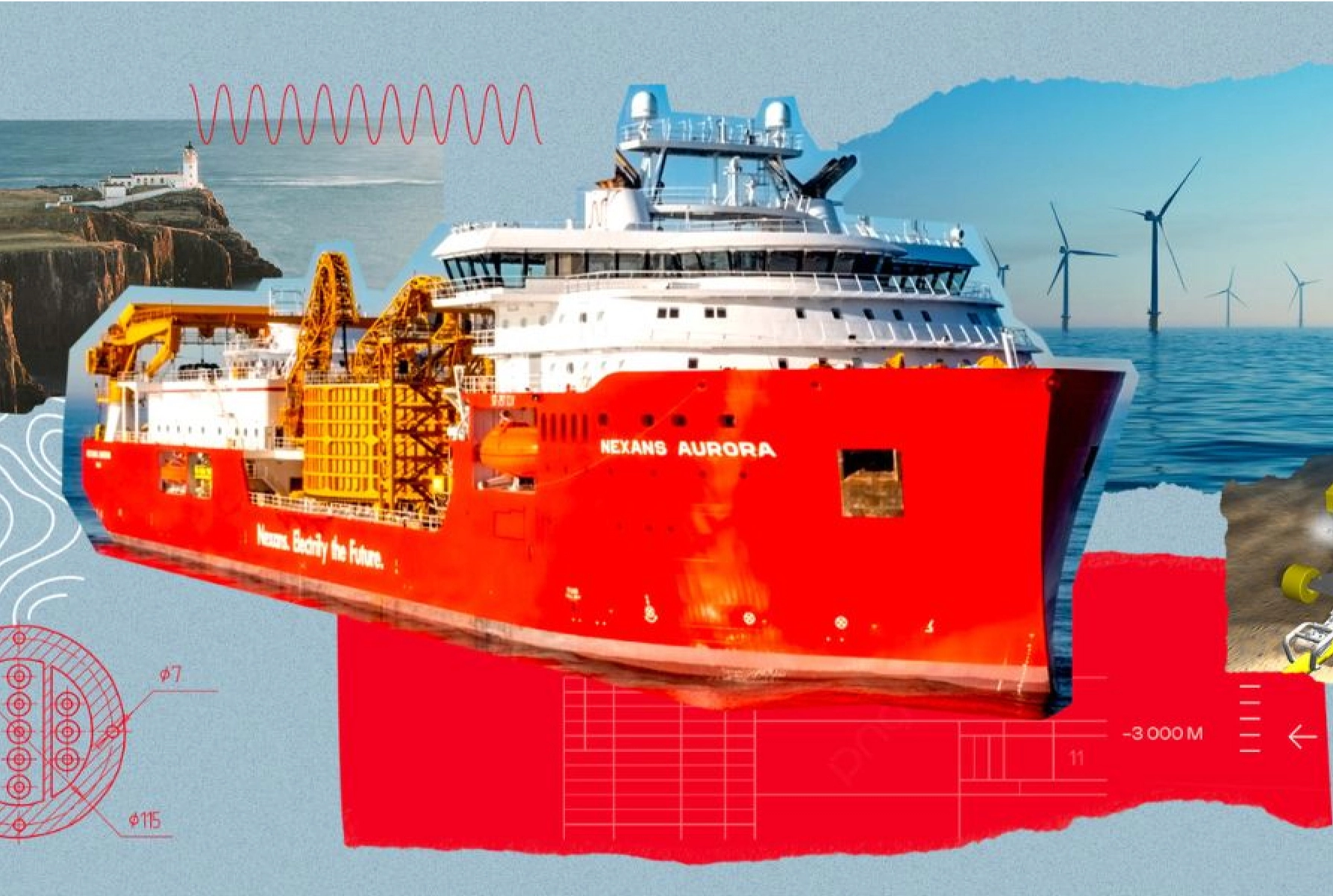
The next time you switch on the lights, take a moment to ask yourself where the electricity comes from. You may be surprised to find that the source is hundreds or even thousands of kilometers away.
As electrical grids span greater distances across sea and land and reach impressive water depths, electricity generation is becoming more renewable and more interconnected.
But that wasn’t always the case.
Without advancements in power cable technology, transportation of energy was limited. The farther electricity traveled along a cable, the greater the loss, which made the transition to renewable energy challenging.
Today, thanks to continued advances in high-voltage direct current (HVDC) cables, renewables are outpacing fossil fuels in the generation of electricity.
HVDC: Powering the future of renewables
Renewable energy grids today – onshore and offshore – require transmission lines capable of transmitting larger amounts of power over longer distances, more efficiently (lower energy loss), at greater sea depths, and able to withstand harsh environmental conditions.
And it is a key driver in the industry’s shift to 525 kV XLPE HVDC (high-voltage direct current) cable technology for large renewable projects – especially commercial offshore wind farms.
The transition to renewable energy requires a new approach to balancing demand and supply of power. Today, the interconnection of neighboring grids is solving this problem. For example, the grid interconnection between Norway and Germany is a perfect example of balancing complementary energy sources for better grid reliability.
HVDC systems make it all possible. In the future, hybrid interconnections and HVDC meshed grids between countries and offshore wind farms will be a reality.
While up-front investment costs and complexity may favor HVAC, the lower transmission loss levels, ultimate power flow control capability, and black start capability may favor the new HVDC alternative.
According to the January 2024 ENTSO-E report – Offshore Network Development Plans, European offshore network transmission infrastructure needs – 14% of the offshore renewables could be connected via dual-purpose hybrid infrastructure in Europe by 2050.
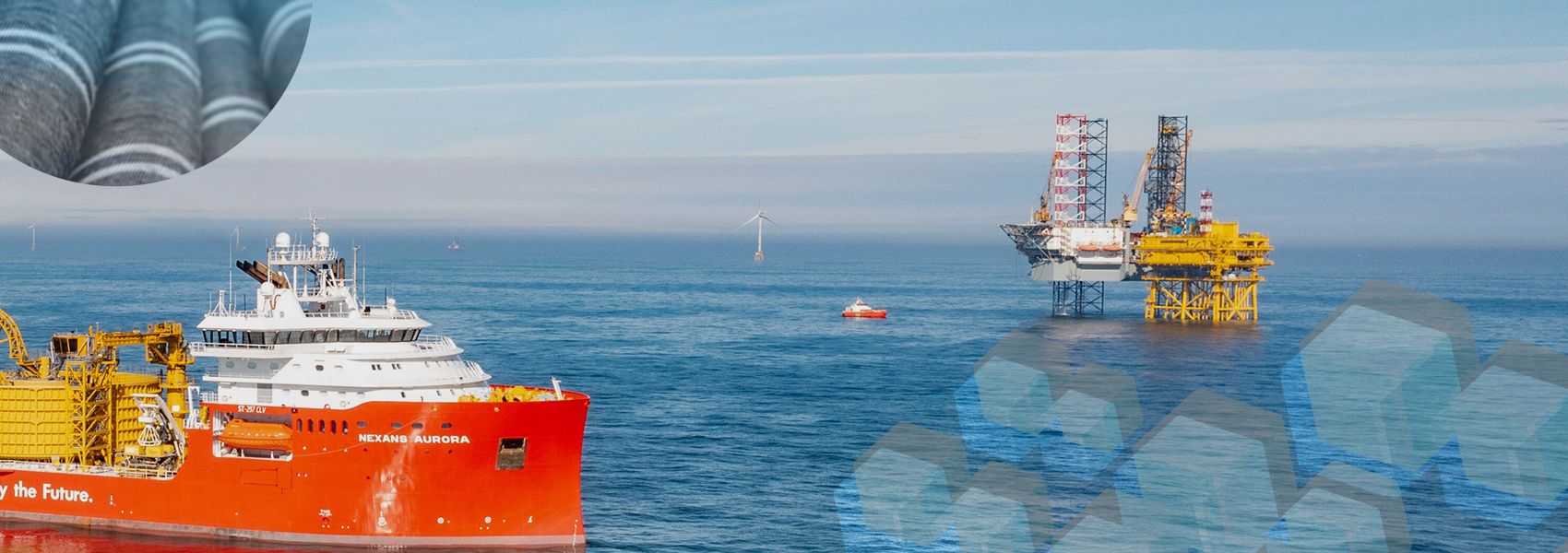
4 cutting-edge advancements in HVDC technologies
Now, let’s delve deeper into the heart of four innovations allowing long-distance connections.
The German TSOs, TenneT, Amprion, and 50Hertz, have pioneered developing and constructing offshore wind farm connections to the grid with HVDC technology.
The latest example is the standardization of 2 GW grid connections of offshore wind farms to the grid using 525 kV subsea and land cable systems. First, a qualification phase was launched for the cable contractors to develop and qualify the technology. Once qualified, projects were awarded for the start of deployment by the end of the decade.
Subsea 525 kV HVDC XLPE – breaking new boundaries in renewable energy
The viability of commercial renewable energy projects is reliant on robust and highly reliable 525 kV cable systems. Achieving this requires increasingly higher quality levels throughout the manufacturing and installation value chain. For cable suppliers, this has meant the expansion of manufacturing facilities, new extrusion towers, creating high-voltage labs, and building advanced cable-laying vessels.
This feat necessitates building upon existing high technology readiness level (TRL) processes and solutions and improving them. At Nexans, cable system know-how plays an integral role in expansion plans and steers the company’s quality control (OC). Examples include:
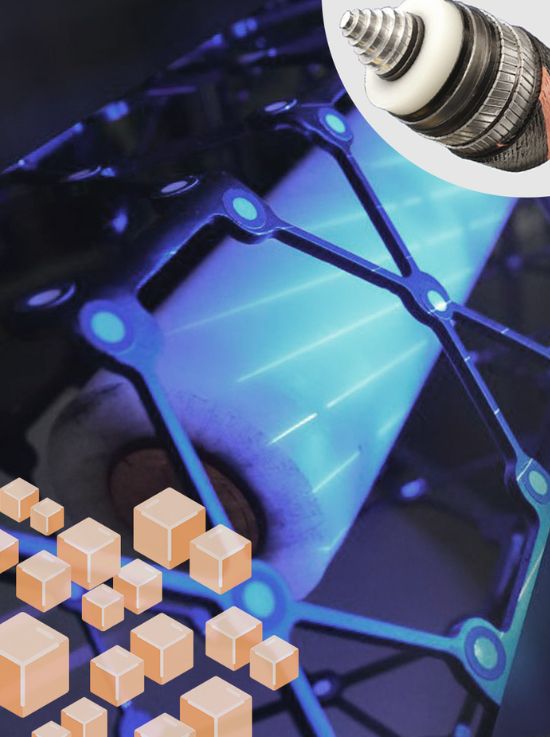
Quality control innovations – SURFICAL
Nexans’ Surface Inspection and Control Algorithms (SURFICAL) are tailored to maximize downstream quality control during on-site installation processes. Using 3D scanning and cable-tailored algorithms, SURFICAL overcomes past cable joint reliability and quality limitations. Whereas in the past on-site crews checked joints visually, SURFICAL ensures defect-free installation.
Achieving the world’s first SF₆-free accessories
In 2023, Nexans achieved the world’s first electrical Type Test on a 525 kV HVDC cable system with SF₆-free accessories. The main benefits of using SF₆-free high voltage accessories include:
- reduced environmental impact
- lower maintenance requirements
- improved reliability.
By eliminating the use of SF₆ gas, cable terminations reduce their potential greenhouse gas emission by 99% and contribute to a more sustainable power grid.
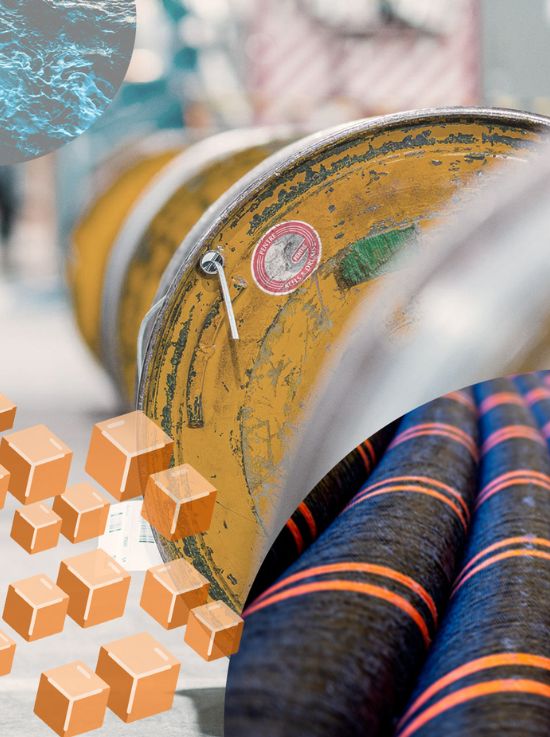
A new era in grid reliability and robustness
While the majority of the 525 kV systems are built upon yesterday’s expertise, new learnings will ensure better grid reliability.
- For example, the technical community recently identified new transient overvoltages (TOV) in HVDC bipole links that are being tested on a large scale.
- Similarly, MTDC systems are expected to come with another set of current and voltage stresses during a fault occurrence, which will have to be tested on the HVDC cable system. While overvoltage tests on cables are not new, as lightning strikes and switching impulse performance tests are commonly included, some TOV waveforms make for a longer overvoltage duration.
While the 525 kV cable transmission level may seem daunting, qualification testing where compressing 40 years of operational stress in one year has shown impressive results. Testing indicates that the insulation system ages very little, and the intrinsic system margins are massive.
Reducing cost per megawatt
The transition to renewable energy relies on interconnected grids transmitting renewable energy across greater distances and at higher power flows. This will reduce the cost per megawatt (MW) and further advance the economic viability of large commercial projects, especially large interconnector projects.
For instance, the same transmission power could be increased in a single circuit rather than two at a lower voltage; dramatically reducing the CAPEX required for a project while having a positive sustainability impact by reducing the use of scarce materials.
Increasing cable voltage will also reduce energy wastage – the higher the transmission kV, the lower the cable conductor losses. Less energy lost to transmission means that remote renewable generation sites will be even more competitive in the future.
Power cables – the backbone of the transition to renewable energy
The transition to renewable energy is essential to reaching global climate targets. At the backbone of this transformation sits the HV power cable.
Advancements in HVDC systems capable of transmitting renewable energy at greater power levels with less loss per MW at greater distances will drive the economic viability of large-scale renewable energy projects, notably offshore wind.

Author
Espen Doedens was born in Diever, Netherlands in 1988. He received the M. Sc. and Ph. D. degrees respectively in 2012 and in 2020 from Chalmers University of Technology in Gothenburg, Sweden. His main research interests are extruded HVDC cable interfaces and DC phenomena. At present he works at Nexans as Product and System responsible for HVDC extruded cable technology.
Did you know that 80% of the total ocean space is too deep for conventional offshore wind farms?
As wind energy takes on a greater role in providing sustainable electricity to millions, harnessing stronger and more consistent winds found farther offshore is critical. In recent years, advancements in high-voltage (HV) dynamic cables, critical to transporting energy back to land, are opening up new opportunities for offshore commercial wind power.
Harnessing wind power in areas previously impossible
A vast, untapped potential lies in harnessing offshore wind power. Although fixed-bottom wind projects currently lead offshore generation, nearly 80% of the world’s offshore wind potential is in waters deeper than 60 meters. This offers a tremendous challenge for the electrical transmission industry.
Yet, during the past thirty years, offshore wind has played an essential role in the decarbonization of energy. According to McKinsey, the growth of offshore wind capacity is projected to reach 630 gigawatts (GW) by 2050, up from 40 GW in 2020.
Since deeper waters are common along most coastlines worldwide, floating offshore wind turbines are crucial for these regions to harness offshore wind energy. Thus, floating offshore wind offers many countries and regions a viable path to electricity decarbonization. But getting this energy back to shore requires robust HV dynamic cables that can withstand the harsh conditions of the seas.
From sea to shore: How tech breakthroughs are powering up floating wind farms
One of the many advantages of placing wind turbines further out from the shoreline is the sheer power of the winds. More powerful and consistent wind speeds equate to a more reliable energy source.
Turning this powerful wind into sustainable energy is possible in part due to new developments in HV dynamic cables and enhancements in floating wind turbines and substation designs.
And it is thanks to these advances that by the end of the decade, large-scale floating wind farms on the West Coast of the United States, France, and South Korea will finally be a reality.
And we’re already seeing this happen. The first commercial floating wind project to be awarded is in France, off the coast of Southern Brittany. This monumental project will, upon completion, be the largest floating offshore wind farm in the world. The 250 MW site will double Europe’s current floating offshore wind capacity.
However, reaching this milestone requires getting the energy back to land where it can be transmitted and used. And this is where HV dynamic export cables are the critical link. To do that requires cables that can withstand deep-water seas. A feat that has taken years to achieve!
4 differences: Breaking new boundaries in HV dynamic cable design
Overcoming new challenges going forward
The oil & gas industry has a long history of using medium voltage (MV) electrical subsea equipment. Today, that same philosophy is being explored for subsea substations. However, HV systems are a different playing field!
Transitioning to HV subsea equipment brings in a lot of additional challenges due to both increased voltage and larger sizes. This generates new challenges for design and handling offshore, combined with even more strict requirements for design tolerances and water tightness.
All HV subsea systems, including cables and potential substations and their connectors, require significant testing and qualification efforts over long time spans. Often, new failure modes arise as we acquire more knowledge about higher-voltage subsea equipment.
When it is possible to install subsea offshore substations or converter stations on the seabed, it will be a game-changer. It will unlock vast new areas for wind energy production, improve efficiency, and contribute significantly to the transition towards a sustainable energy future. For example, this advancement will significantly enhance the cost efficiency of electrical export, ultimately reducing costs and optimizing resources.
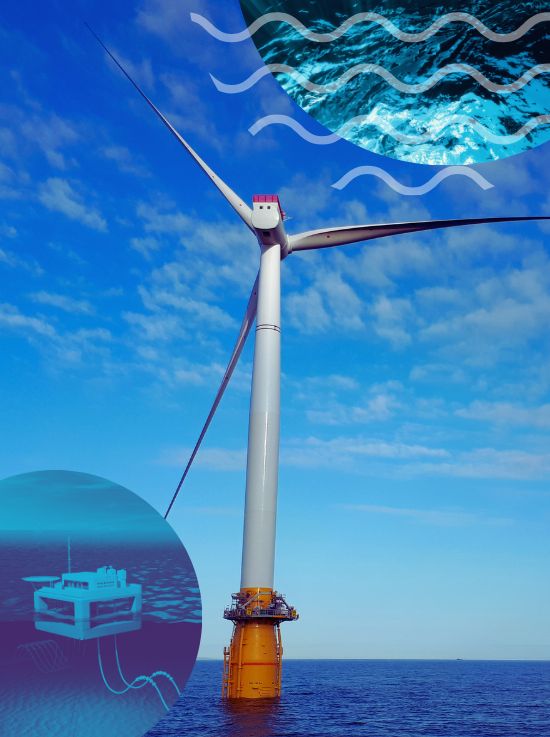
Driving the critical link in floating wind power
The largely untapped deep-water areas open up new opportunities for floating wind farms. A key link to the future of floating wind is the vital cables required to transport energy to shore. Nexans is driving innovative cable technologies and design methodologies to further the development of commercial floating wind farms.
- A long track record in dynamic hybrid cables is led by the Group’s experience in materials, modeling, and software development. Dynamic power umbilicals & DEH systems experience, combined with its HV subsea cable expertise, this gives a unique combination of design and manufacturing know-how, allowing to simulate, test, qualify, and manufacture HV dynamic cables.
- In 2021, Nexans made a major breakthrough by qualifying the first 145 kV dynamic cable for 1300-meter water depth. Selected for the Jansz-lo project, this innovative cable is leading the way for floating offshore wind projects.
Growth of floating wind farms in the years to come
The vast open seas hold great potential in the world’s quest to decarbonize electricity. Floating wind farms, farther out and deeper, will play an increasingly important role in the battle against climate change.
Major advancements in HV dynamic capabilities play a critical role in achieving the commercial success of floating wind farms. Nexans’ groundbreaking 145 kV dynamic cable capable at 1300 meters opens up new opportunities for deep sea projects in harsh water conditions. This innovation is crucial for the future of commercial floating wind farms.
According to an August 2023 Global Wind Energy Council (GWEC) report, the floating wind market will accelerate by the end of the 2020s, with 11 gigawatts (GW) installed by 2030 and 26 GW by 2032.
Starting in 2031, floating wind installations will constitute over 10% of annual offshore wind installations, a notable achievement given the rapid expansion of offshore wind overall.
This growth will significantly contribute to adding decarbonized electricity generation to power grids, supporting global efforts to reduce carbon emissions, and the transition to sustainable energy sources.
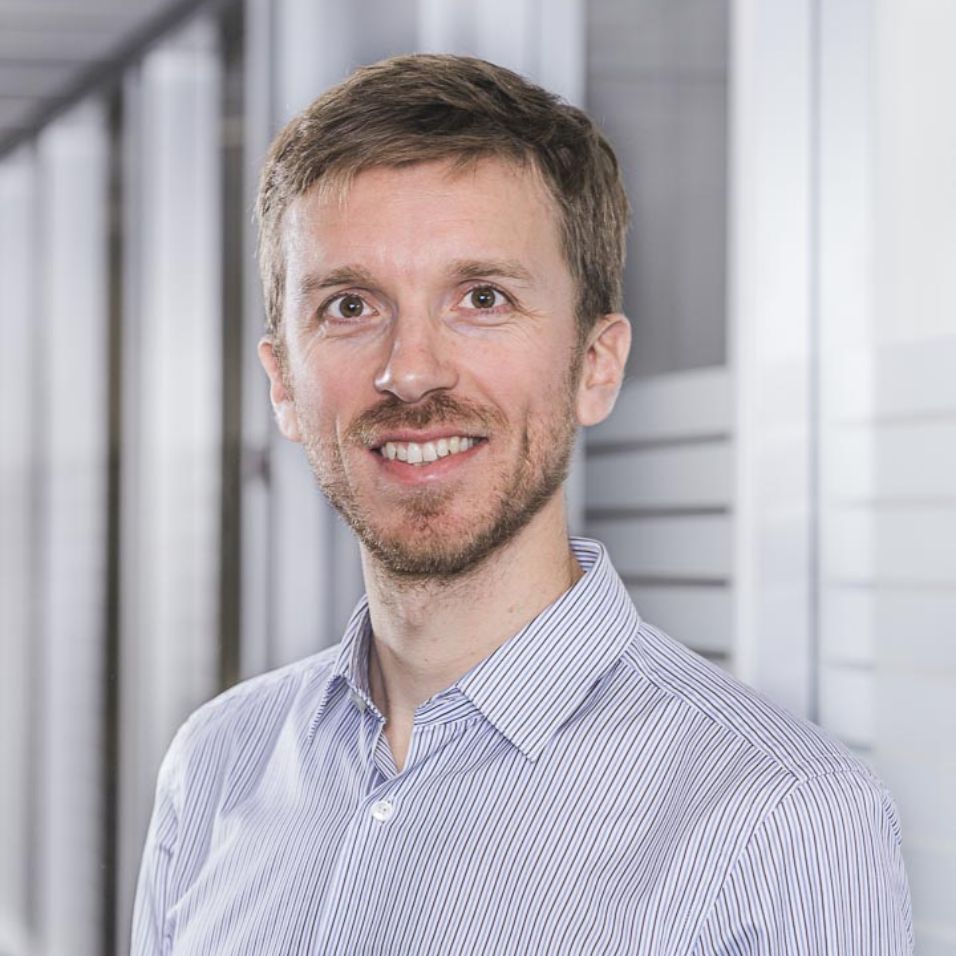
Author
Maxime Toulotte is the Markets & New Solutions Director of Generation & Transmission Business Group in Nexans, where he has the responsibility to develop and maintain relations with technical and engineering departments of clients and partners for subsea high voltage cables.
Maxime has held several positions as Sales & Tender Manager and Lead Engineer for high voltage submarine cable system projects.
Maxime holds a Master’s degree in Electrical Engineering from the Grenoble Institute of Technology, France.
Power grids are undergoing a monumental transformation. Driven by the energy transition, vast offshore wind farms are sprouting across the globe, promising a more sustainable future.
Connecting these remote parks to the mainland grid requires a crucial but often overlooked hero: the submarine power cable.
Imagine these cables as the silent arteries of the energy sector, carrying enough electricity to light entire cities. Their importance is undeniable – a single high-voltage cable tripping can put energy security at risk.
These underwater giants, stretching for hundreds of kilometers, face a unique set of challenges. Unlike their above-ground counterparts, they’re largely hidden from view, making proactive maintenance a critical and complex task.
Yet, recently, a declaration announcement emanating from six North Sea countries and NATO has emphasized the significance of infrastructure security and robustness.
This is where cable monitoring comes into play.
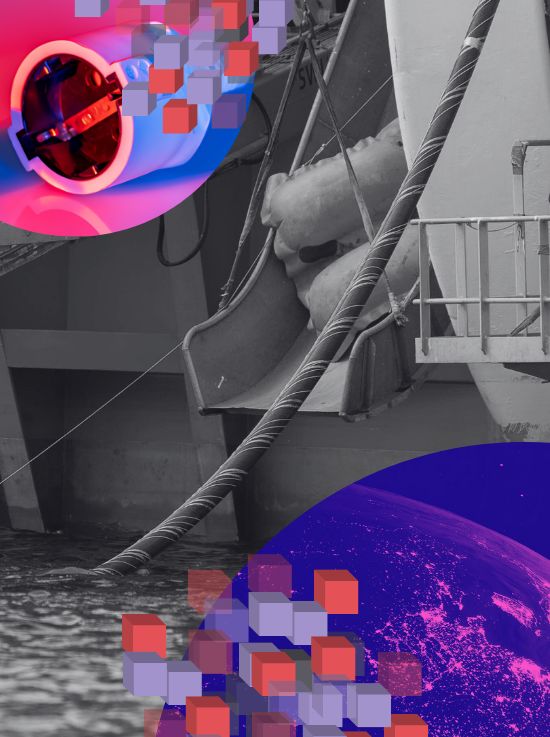
Why subsea cables monitoring matters
Think of it like this: you wouldn’t ignore a persistent knocking sound in your car engine. If a strange rattle might not be a cause for immediate alarm, it’s still a signal to get it checked before it develops into a major breakdown. In the same way, cable monitoring allows us to diagnose potential problems with subsea cables before they morph into a crisis.
A sudden subsea cable failure will disrupt the delicate flow of electricity within a grid and could trigger various event, ranging from minor frequency shift to more serious issues like brownout, where voltage dips and appliances struggle to function properly. In extreme cases, it could even lead to a complete blackout – a situation where entire regions are plunged into darkness, disrupting everything from traffic lights to hospitals.
By constantly monitoring the health of subsea cables, we gain real-time insights into any potential issues. These insights allow grid operators to take preventative actions, such as rerouting power or scheduling maintenance, before a minor problem escalates into a full-blown emergency.
Monitoring of subsea cables: 3 main challenges
Due to the increasing reliance on offshore power sources, grid operators are being faced with changes and challenges. Here’s a closer look at some of the key concerns:
1. The end of a decentralized past
Traditionally, cable health data was scattered across individual local control rooms and equipment, making it nearly impossible to get a holistic view of the system. It was like having ten different doctors analyzing your health, each with their own reports and interpretations.
Thankfully, the tide is turning. We’re witnessing a shift towards centralized platforms that consolidate data from various sources, offering a comprehensive view and enabling faster, more informed decision-making.
2. The data deluge: Making sense of the noise
But the journey to a truly robust monitoring system isn’t without its obstacles. One major hurdle is the sheer volume of data generated by an array of sensors. Imagine being bombarded with continuous data streams from a thousand sensors – how do you identify a subtle change that can lead to a threatening event?
Another hurdle arises from the fragmented nature of the monitoring landscape. Different vendors often use proprietary technologies, making it difficult to integrate data from various monitoring systems. This creates a tangled web of information, hindering efficient analysis. The ideal solution lies in open platforms that seamlessly integrate with diverse monitoring technologies, providing a unified view of cable health.
3. The limitations imposed by longer interconnections
Subsea interconnectors, the power cables linking distant grids across vast stretches of ocean, pose a unique challenge for traditional monitoring techniques.
Take, for instance, the ambitious Great Sea Interconnector project, a planned high-voltage cable stretching a staggering 900 kilometers to connect the power grids of Greece and Cyprus.
At such immense distances, conventional monitoring methods using optical fibers suffer from signal attenuation – essentially, the message gets weaker as it travels, making it harder to detect issues.
To overcome this challenge, the integration of technologies akin to those used in transoceanic cables, such as amplifiers, is essential. Amplifiers can boost the signal strength at regular intervals along the cable, ensuring that monitoring systems maintain accurate and reliable communication.
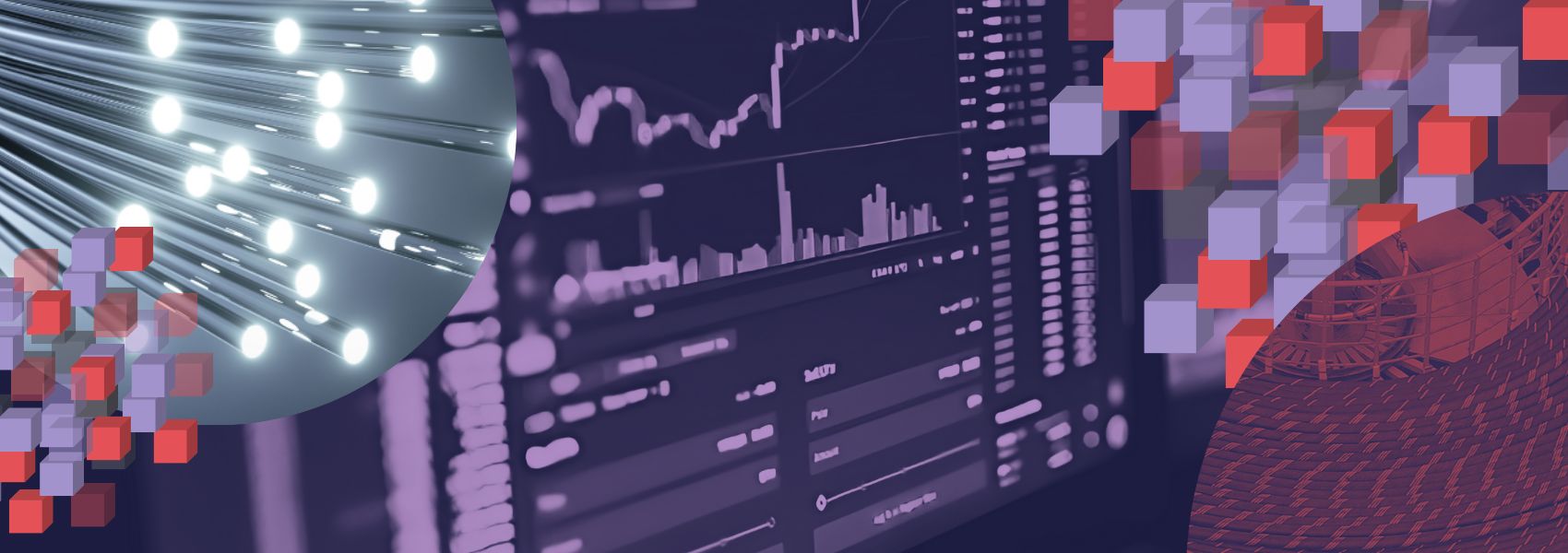
5 advanced techniques for subsea cables monitoring
Thankfully, the world of cable engineering can count on plenty of solutions. Here are some of the cutting-edge technologies playing a vital role in safeguarding the health of subsea power cables.
Monitoring and the revolution of artificial intelligence (AI)
Of course, AI is among the most promising revolutions for the monitoring of subsea cables.
Indeed, the sheer volume of data generated by advanced monitoring systems can be overwhelming. This is where AI steps in, helping to:
- Filter Out Noise and Identify Threats: By analyzing complex data patterns, AI can effectively distinguish between background noise and real threats. This ensures that operators focus their attention on the most critical issues.
- Predictive Analytics: AI can leverage historical data and real-time sensor readings to assist in identifying potential problems before they even occur. This allows for preventative maintenance and minimizes downtime.
The road ahead: Monitoring powered by constant innovation
Imagine a user-friendly cockpit that displays real-time data, analyzing failure modes, and proposing remediation actions for all your cable assets in single place: this, in essence, is the future of cable monitoring.
Comprehensive cable monitoring solutions are paramount. A centralized approach not only simplifies cable management but also empowers operators to make informed decisions quickly and efficiently.
Nexans, at the forefront of these innovations, has developed a solution that isn’t just an abstraction layer: it is a versatile data platform, with state-of-the-art digital frameworks, intuitive dashboard and harmonized analytics that brings the cable data management to the next level. It integrates information from various sources and presents a clear picture of the network’s health.
Built to scale, it adapts seamlessly to the growth of the grid. Whether through on-premise deployment or cloud-based access, this solution offers flexible options. Prioritizing cybersecurity, the platform utilizes the latest technologies and maintenance processes to safeguard critical data.
The energy transition depends on the silent guardians of the grid – subsea power cables. As we harness the power of offshore wind farms, robust cable monitoring becomes an indispensable tool. By overcoming the challenges of data management, signal interpretation, and technological fragmentation, we can ensure the health and longevity of these critical underwater connections.
Innovative monitoring technologies can help the silent heroes under the sea to continue to play a vital role, ensuring the lights stay on and our cities vibrate with sustainable energy.
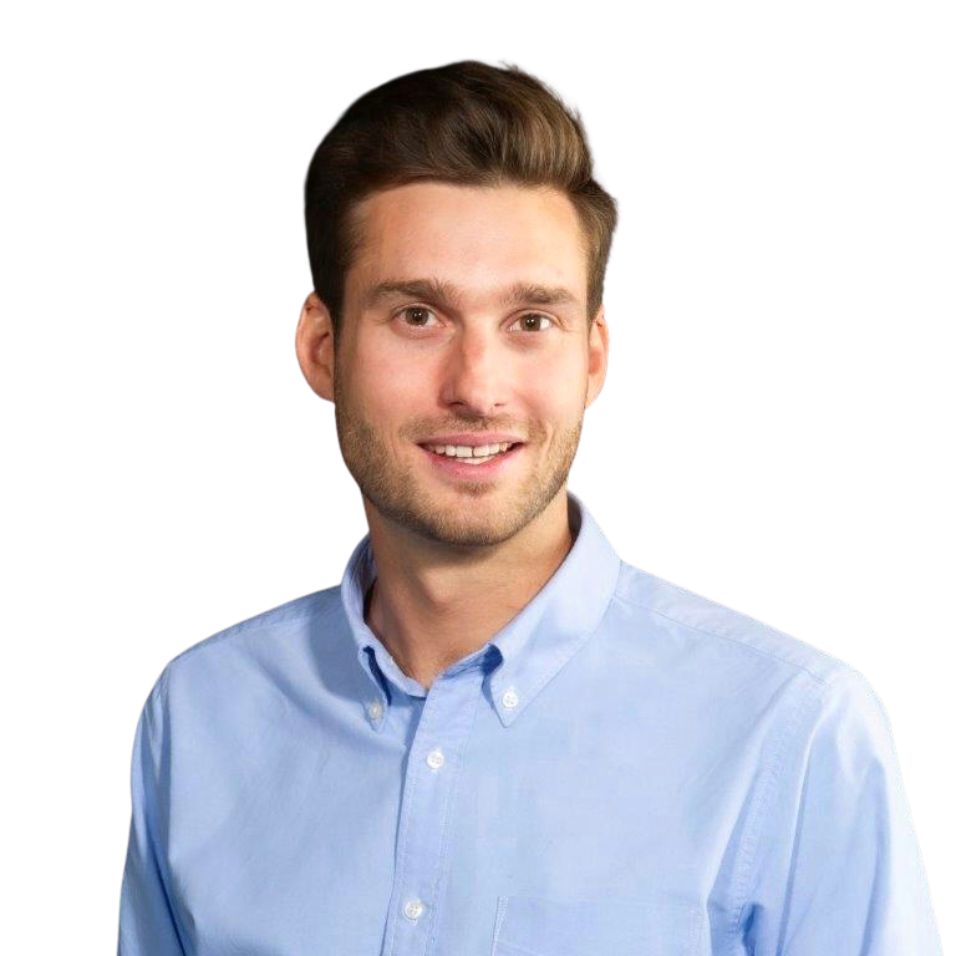
Author
Aymeric André works as New Solutions Manager at Nexans within the Sales & Marketing department of the Generation & Transmission Business Group.
In 2019 he joined Nexans Services and solutions team within the Innovation Service and Growth Department as a Design Lab Manager for asset monitoring to help enhance the company’s digital offers.
He has previously worked at the SuperGrid Institute where he led a research program on high voltage subsea technologies.
Electrification, particularly from renewable sources, is playing a pivotal role in the world’s quest for net zero emissions. And as we move towards a more electrified future, it’s crucial to acknowledge the environmental impact of the very cables that power our lives.
The demand for subsea cables that can safely and efficiently carry the growing current is surging. As innovative technologies are reaching new heights in their ability to transmit sustainable energy at greater volumes, distances, and depths, ensuring their sustainability throughout their life cycle is equally important.
Let’s dive into the innovations in electrical transmission that are unquestionably promoting this shift.
Subsea cables: the need for a sustainable mindset
But first, there are two reasons why the question needs to be raised.
1. Cables’ components
The environmental footprint of the cables’ materials demands our attention. These are the obvious environmental costs it takes to electrify the future.
Above all, the conductor, which channels the electrical flow, is composed of copper or aluminum and constitutes a significant part of the overall GHG emissions of subsea cables. Much of this is due to the energy required in producing and purifying the metals, which is why it is essential to use renewable energy in the extraction process to reduce the environmental impact.
2. The importance of sustainability in a resource-constrained world
Did you know electrical wire and cable can contain up to 80% copper?
Known as ‘the metal of electrification,’ copper is paramount in the production of cables. The metal is excellent for conducting electricity efficiently: its unique properties allow for a smooth flow of electrons, which minimizes energy loss in transmission lines.
Yet, due to the growing focus on electrification, global copper demand is expected to reach 39 million tons in 2030 (compared with 13 million tons in 1995 and 29 million tons in 2020). And possibly, at the same time, it might become increasingly scarce. Furthermore: its excavation and mining come with its own social and environmental challenges. Co-existence with other industries such as fisheries as well as local communities which might be adversely affected by mining can limit access to potential resources.
Let’s now explore the solutions and innovations that are key to help us mitigate the environmental impact of subsea cables.
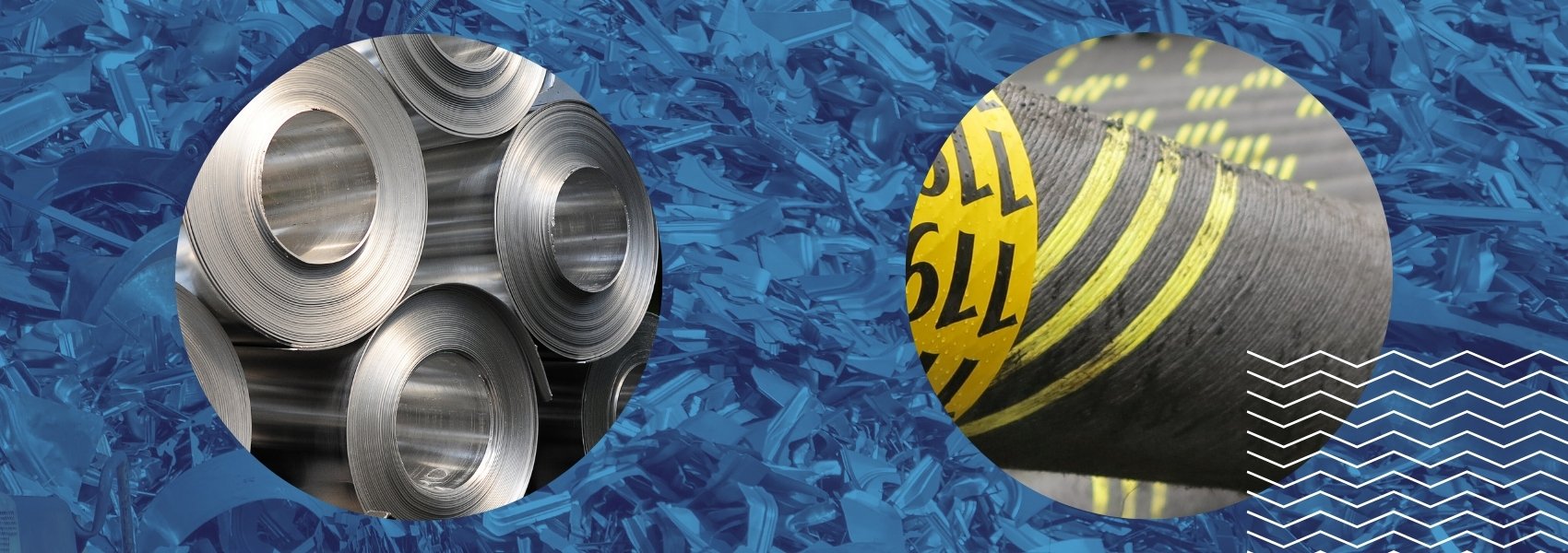
3 innovations for sustainable subsea cables
The future – moving to a sustainable mindset
Nexans positions itself at the forefront of this impetus. For example, the Group’s casting facilities in Canada, France, and Peru reused roughly 19,700 metric tons of copper scrap in 2022. In 2008, Nexans and Suez formed the joint venture RecyCâbles as a complete cable recycling solution. Since its inception, it has become a European leader for cable recycling and recovery.
Here are three concrete examples of current innovations that are leading the way:
SF₆ replacement and GIS terminations
Replacing SF₆ as insulating medium in cable terminations, with alternative insulating gases (such as GE’s g³) or with dry-type solutions, is critical. This would reduce the GWP, with more than 99 percent, in any event of accidental gas emission. Converter manufacturers are also currently developing switchgears using alternative gas to SF₆, so this gas can be substituted in the complete HVDC cable systems.
The advantage of using GIS terminations is twofold, because GIS terminations also allow a major reduction of space needed in the offshore converter stations, which leads to significant reduction of converter platform size, and consequently of steel used for its construction.
The OceanGrid Project
Innovative research initiatives are instrumental in seeking more sustainable and viable interconnectors. With the OceanGrid Project, research is being carried out on a new aluminum alloy aiming to advance the deployment of profitable offshore wind farms in Norway in 2030 – 2050.

The AluGreen consortium
In the AluGreen consortium, Nexans leads the exploration of introducing end-of life conductor materials in new subsea cables. The consortium draws from the full aluminum value chain in Norway which sets the stage for piloting full circular business models.
The world is electrifying, and the cables that carry this energy surge need a sustainable upgrade.
Subsea cables are crucial for efficient transmission of renewable energy offshore. Yet, they can have a significant environmental footprint.
Traditional materials and production methods create challenges; however, innovation, from recycling to new technologies, is paving the way for a more sustainable future.
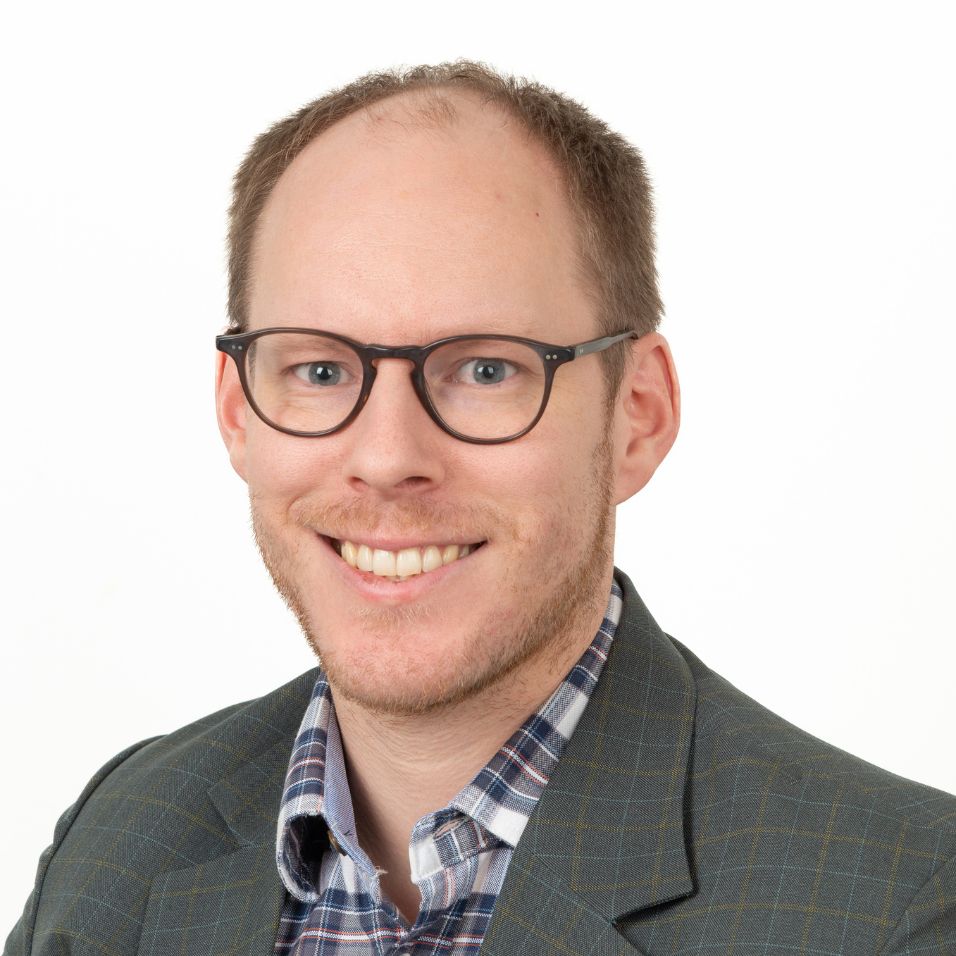
Authors
Audun Johanson is an R&D Project Manager & New Opportunities in Nexans’ Generation & Transmission Business Group, where he drives technology development for future energy transmission with a particular focus on floating wind and circularity.
He has joined Nexans 10 years ago with an educational background in material science from the Norwegian University of Science and Technology, Norway.
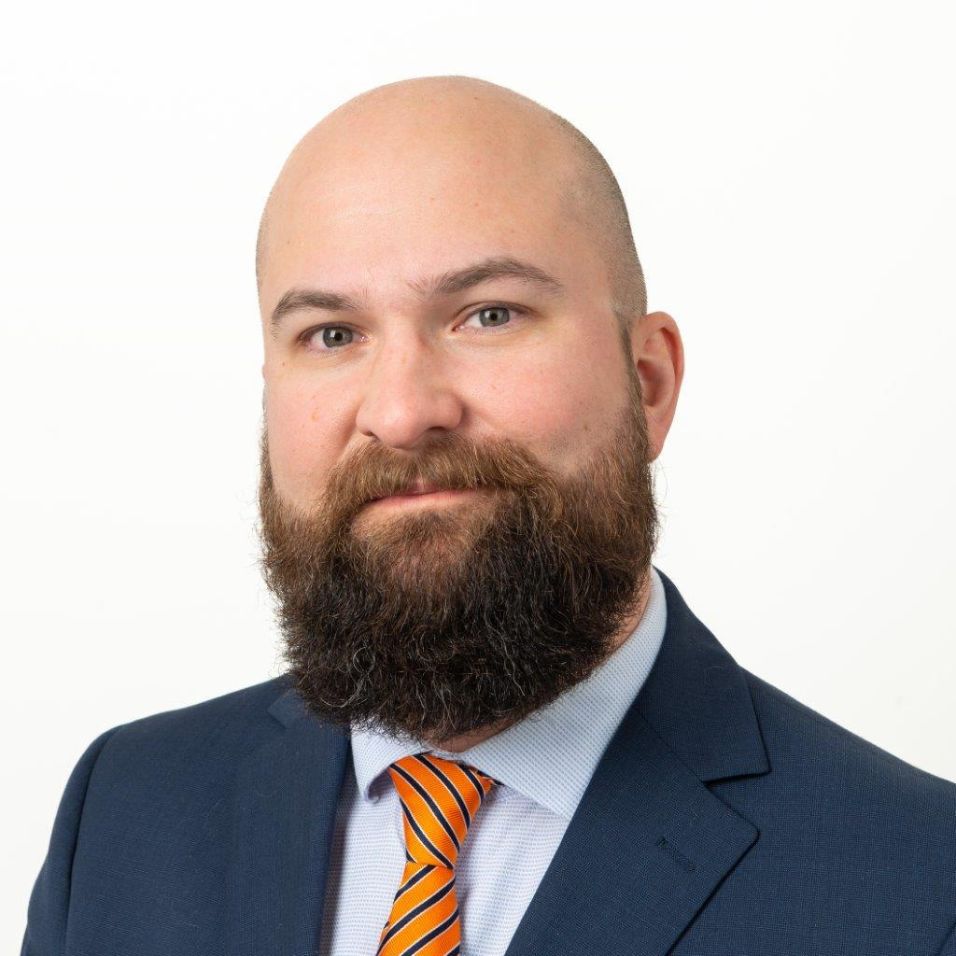
Nils-Bertil Frisk is the Discipline Responsible for HVDC Extruded Accessories in Nexans’ Generation & Transmission Business Group, where he has the responsibility to develop, maintain and standardize HVDC Extruded cable accessory portfolio.
Nils-Bertil started in Nexans R&D department 10 years ago with a main focus on HVDC Extruded accessories.
Nils-Bertil has a Master’s degree in Electrical Power Engineering awarded from Chalmers University of Technology, Sweden.
Imagine a giant sea serpent made of copper and steel, winding along at a depth of 3,000 meters under the sea. No, it’s not a mythical sea creature, it’s an interconnector cable!
You are no doubt already familiar with subsea fiber optic cables, the technology making it possible for you to read this article. Yet the underwater depths also host far larger cables, able to transmit electricity from one country to another.
What is an interconnector?
Routed under the sea, these high-voltage cables play the role of invisible highways, taking electricity from one country to another.
They measure up to 300 mm in diameter and can weigh up to 140 kg per meter… for a total weight of up to 9,000 metric tons! We’re talking here about gigantic structures that can weigh as much as the Eiffel Tower.
To imagine what’s inside, think of a big sushi: the cable body is made of copper and sometimes optical fiber, protected by an armor of thick steel.

These subsea cables are manufactured in ultra-modern plants, able to assemble the various components with millimetric precision. They are then transported on cable-laying vessels, which deploy them on the seabed.
This operation is a real technological feat, making it possible to transfer power across seas and oceans, in order to support the energy transition.
What are the advantages of subsea interconnectors?
Let’s just take a step back in time: the first interconnections between national power grids took place two decades after World War Two.
Today, Europe is the most advanced continent in terms of interconnections. Its highly sophisticated network relies in part on these subsea cables.
So, what are the advantages of these interconnections?
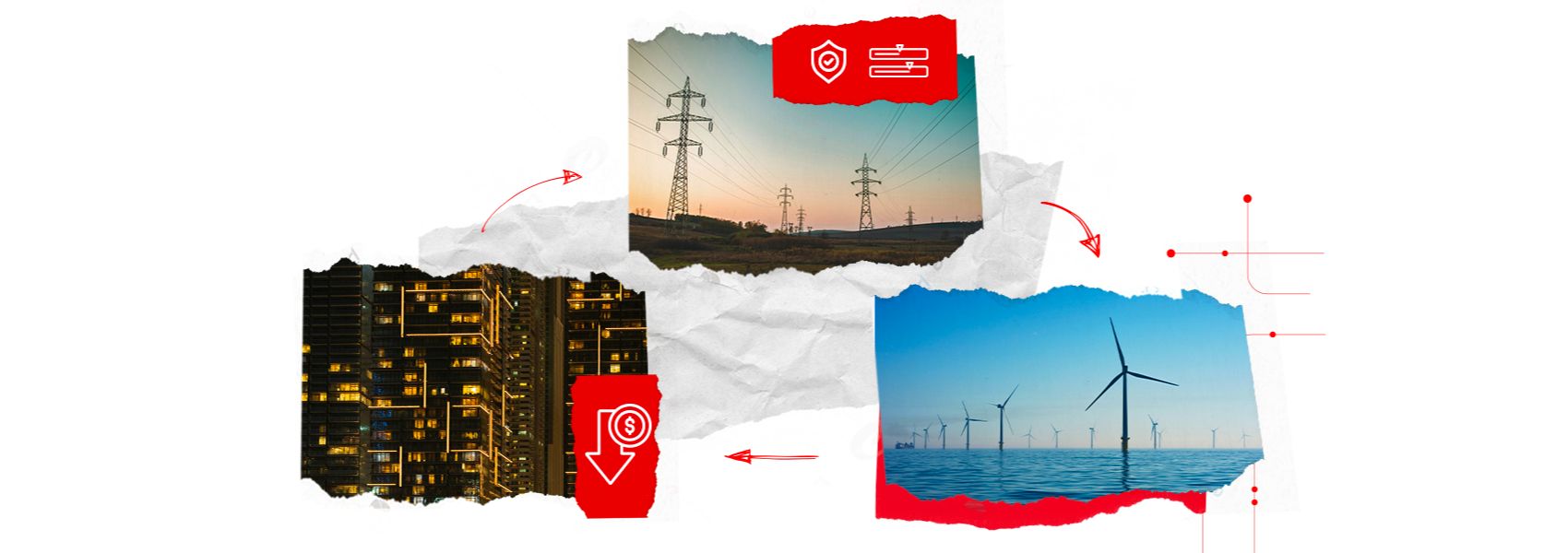
A fast-growing interconnection market
It is no surprise to see the offshore wind and interconnection markets expanding at a rapid pace. Major investments will be needed wherever the level of interconnection remains insufficient.
Subsea cables are becoming an increasingly common choice, not only in America and Europe, but also elsewhere in the world. In September 2023, for example, the grid operators of Greece and Saudi Arabia signed a strategic agreement setting up ‘Saudi Greek Interconnection”, a joint venture to link their power grids.
Forecasts for the European interconnection market
By 2030
15%
of each European country’s electricity
production should be exportable under
a newly established system
97
interconnection projects implemented
in Europe, with 21
at the development stage
+72,000 km
of HV cables to be installed
between 2020 and 2030
No interconnections… without cable-laying vessels
Cable-laying vessels transport the cables and deploy them on the seabed. Measuring over 100m in length in some cases, these steel monsters are high-tech gems and a key component of the interconnection process.
A growing number of new-generation vessels are currently being developed to meet increasing demand for electrification, particularly in Europe and the US.
Among the most advanced cable-laying vessels is Aurora. Named after the Roman goddess of the dawn, this giant of the sea is 150m long. A truly exceptional vessel equipped with state-of-the-art technology, Nexans Aurora is capable of laying ultra-high-voltage subsea cables over thousands of kilometers and at abyssal depths. Its role is to connect offshore wind farms to onshore grids, and deliver the power generated by the wind to our homes.
Aurora is Nexans’ second cable-laying vessel. The Group is in the process of adding a third vessel to its fleet: Electra.
Electra in figures
2026
Launch
Design & comfort
Greater capacity
than Nexans Aurora
3
turntables
13,500
metric tons loading capacity
up to
4
cables can be laid at a time
A giant of the Mediterranean: The Great Sea Interconnector
Among the most impressive subsea interconnection projects is the Great Sea Interconnector project (formerly the EuroAsia Interconnector). This 2-gigawatt giant is set to become the world’s longest and deepest high-voltage direct current (HVDC) subsea cable. Measuring 900 kilometers in length, deployed at a depth of over 3,000 meters, it will link the coasts of Greece and Cyprus in a never-before-seen electrical embrace. The Great Sea Interconnector symbolizes a new era in energy interconnections. Whereas Cyprus was isolated from the European grid, it will be connected to a stable and diversified energy source, promoting the integration of renewable energies and reducing its dependence on fossil fuels. Nexans Group was tasked with manufacturing this subsea interconnector, the longest and deepest in the world. This is a challenge on an exceptional scale: building the Great Sea Interconnector required immense resources and exceptional logistics, allowed by Nexans’ ability to produce whole kilometers of cables in its ultra-modern plants, for shipping and deployment in the depths of the Mediterranean.
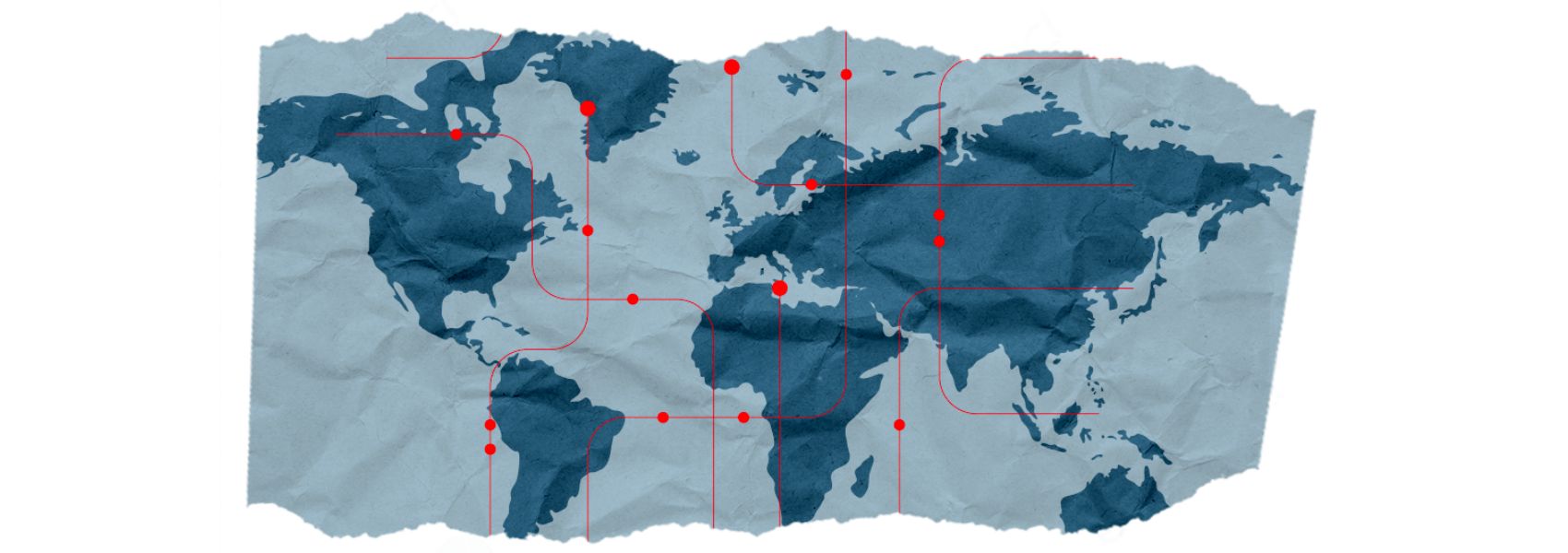
So, in short… Subsea interconnection cables are invisible giants, energy highways winding along the seabed.
As such, they have a crucial role to play in the global energy transition: enabling the exchange of electricity between countries, promoting the integration of renewable energies, securing supplies and contributing to lower prices.
These cables represent both a technological feat and a colossal level of investment. Their development is part of an ongoing dynamic. Subsea cables are a key part of efforts to address climate change and to build a more sustainable energy future.
Renewable sources of electricity become an increasing and exceedingly important factor in the energy equation. Global annual renewable capacity additions increased by almost 50% to nearly 510 gigawatts (GW) in 2023, the fastest growth rate in the past two decades, marking a major step forward in the reduction of fossil fuel power. Moving to renewable energy is vital to decreasing greenhouse gas emissions and aligning with the 1.5 Celsius climate target set in the Paris Agreement.
Even as renewable energy generated a record 30% of global electricity in 2023, furthering the growth of renewable energy relies heavily on grid interconnection.
Grid interconnection – the critical link to energy security
Interconnections provide the optimal way to ensure energy security across regions and continents:
- When grids are interconnected, surplus energy from one region is easily transported- via the interconnected power grid – to where electricity is needed. This ensures energy security across the interconnected grids and avoids reliance on fossil fuels when renewable energy cannot meet local demand.
- By equalizing demand and supply across interconnected grids, excess power is more readily available to areas with increased demand, thus ensuring energy price stability and future renewable investments.
- The harnessing of electricity across grids goes beyond adjacent regions to include the interlinking of power grids across continents and islands and offshore renewable energy sources. Deep water, once a barrier to interlinking grids, is less of an issue thanks to innovations in cable design, new materials and alloys, and cable installation and maintenance advancements.
Cable-laying vessels, the high-tech gems of the interconnection process
A growing number of new-generation cable-laying vessels are currently being developed to meet the increasing demand for electrification and interconnections.
Among the most advanced ones is Nexans Aurora (and in the future Nexans Electra), a 150-meters long giant, equipped with state-of-the-art technology. It is capable of laying ultra-high-voltage subsea cables over hundreds of kilometers and at abyssal depths.
Thanks to those steel giants, interconnections allow us to overcome the reliance on fossil fuels. Here are four innovations in deepwater HV cables that are highly contributing to tackling this challenge.
4 innovations for subsea cables that are game-changing
1. Deep sea grid interconnections – from megawatts to gigawatts
The interconnection of grids is not only reaching impressive depths, but their capacity has also gone from hundreds of megawatts to gigawatts.
To date, the deepest installed HV cable system is the SaPeI interconnector, stretching 435 kilometers, linking Sardinia and mainland Italy, reaching 1,640 meters below sea level.
One revealing example of this revolution is the Tyrrhenian Links project, currently under construction. It will connect Sicily with Sardinia and the Italian peninsula. It will be installed at a record-breaking 2,200 meters deep, for a transmission capacity of 1,000 MW. Achieving this is possible thanks to advances in high-voltage direct current (HVDC) systems, which can transmit larger amounts of power over long distances.
If this technology is already available for shallow waters, engineering challenges arise when increasing the water depth.
2. Mass-Impregnated (MI) undersea cables – decades-long reliability track record
Mass-impregnated cables’ first commercial use was in 1954 for the Gotland HVDC Link to connect the Island of Gotland to mainland Sweden. Since then, mass-impregnated cables have been the primary choice for subsea HVDC interconnector projects requiring voltages surpassing 500 kV over long distances and extreme depths.
Simply put, a MI undersea cable is a type of HVDC cable specifically designed for underwater applications. Here is the breakdown:
- Construction: it is made with layers of high-density paper tapes wrapped around the conductor. These tapes are then impregnated with a special, high-viscosity compound. This compound is key – it’s thick and doesn’t flow easily, even if the cable is damaged.
- Application: it is used for transmitting large amounts of electrical power over long distances underwater. They are particularly useful for applications exceeding 500 kV DC and long distances.
MI cables offer three main advantages that make them innovative for undersea applications:
- Reliability: The high viscosity compound prevents leakage even if the cable is damaged, making it more reliable for underwater use compared to older designs.
- Durability: cables installed decades ago are still operational today, demonstrating their long lifespan.
- Depth capability: they can be used for extreme depths with proper design features.
Overall, MI cables are a well-established and trusted technology for transmitting large amounts of power underwater, making them a key innovation for subsea power transmission.
Breaking even new barriers to deep sea cable depths will be the Great Sea Interconnector project. Reaching depths of up to 3,000 meters in some areas, the project will connect Israel, Cyprus, and Greece via Crete. Stretching 900 kilometers from Crete to Cyprus, the 1,000-megawatt, bi-pole cable will bolster energy security and facilitate electricity exchange between the countries.
3. Overcoming subsea cable challenges – new design approaches
The main challenge in using MI technology in subsea cables however is the elongation of the insulation system during deployment and retrieval.
There are many ways this can be overcome. The most prominent is through cable design, conductors, materials, or installation methods.
Additionally, 500+ kV extruded cable designs are also being developed. A major advantage of extruded cable design is its ability to sustain greater elongation compared to MI cables. A challenge for extruded design is the need for effective water blocking in the conductor in the case of damage to the cable. At 3,000 meters below sea level, the pressure is so great that if the water is not blocked in the conductor, it can easily penetrate tens of kilometers into the cable, leading to costly repairs.
4. Monitoring and repairing subsea cables: a priority
Repairing and retrieving subsea cables at extreme water depths is a significant challenge. To avoid power outages and grid failure, contingency plans are crucial. Inspection, maintenance, and repair (IMR) agreements are vital to minimize failure risks through proactive inspection and maintenance, thus reducing incident response time.
Even as barriers to deep sea depths are reached, monitoring the health of subsea cables will increasingly be a vital part of ensuring the reliability of interconnected grids.
The future – interconnected grids driving renewable electrification
Nexans is deeply involved in the electrical transmission revolution that is going on.
In fact, the Group has been playing an essential role for a long time. In 1977, Nexans deployed its first HVDC MI cables for the Skagerrak subsea interconnector between Denmark and Norway. Almost 50 years later, the original cable system is still in use. Today, its expertise in building, installing, and repairing deep sea HVDC systems spans MI and extruded technologies.
Its most monumental undertaking is currently crafting the world’s longest and deepest subsea interconnection: The Great Sea Interconnector. This colossal project symbolizes a new era in energy interconnections and demanded immense resources and logistical mastery.
Innovation is the lifeblood of deep sea grids. For this sustainable future revolution to reach its full potential, robust and far-reaching interconnectivity is paramount. Deep sea grid interconnectors are the invisible threads weaving a global energy tapestry. Challenges remain, but solutions are on the horizon.
Deep sea grids are not simply cables on the ocean floor; they are the lifelines of a safer energy landscape. They are the physical manifestation of a global commitment to a sustainable future, a future powered by the boundless potential of renewable energy.
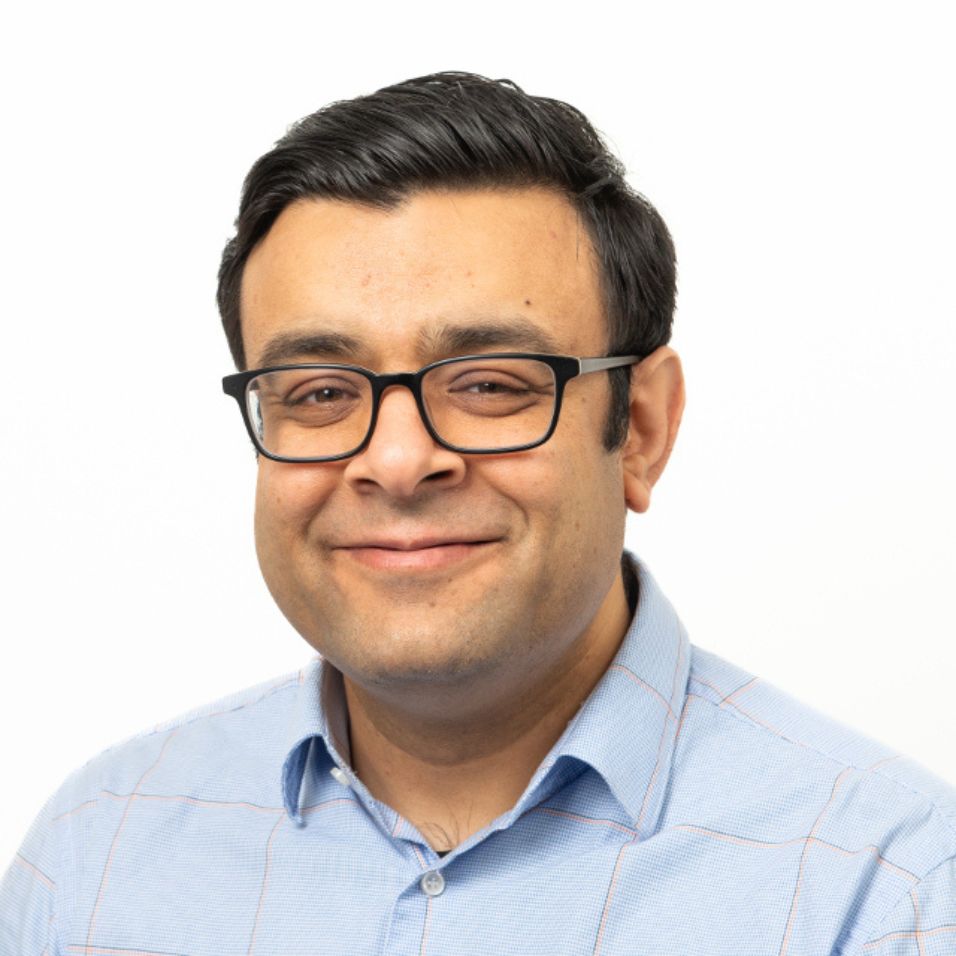
Author
Robin Sangar is an R&D Engineer in the Generation & Transmission Business Group in Nexans, working to challenge the status quo with novel solutions and bringing together people from across disciplines and the organization to solve problems.
Robin has held several positions in Nexans, from tender to project and now R&D.
Robin holds a Masters degree in Experimental Physics from the Norwegian University of Technology and Science, Trondheim.
Faster, higher, stronger – together is the motto of the Olympics, but it can also apply to the changes happening in the electricity transmission and distribution industry.
As decarbonization of energy takes on a heightened importance globally, it will take a unified approach to reach net zero by 2050. To do so will mean eliminating fossil fuel combustion and transforming power grids to accommodate intermittent renewable energy.
Rejuvenation of the grid that a decarbonized and electrified world needs differs significantly from the ones built post World War II and on which we still rely today. Modernization and newer storage technologies are crucial in decarbonizing electricity. But equally important are the connections of supply from one electric network to another to ensure energy reliability and stability and transition the world to renewables.
Thus, according to a report published by the International Energy Agency, the world must add or replace about 80 million km of grids by 2040, equal to all grids globally today, in order for countries to meet their climate goals and to achieve energy security priorities. Considering only offshore wind in Europe, 48 000 to 54 000 km of HV cable route length shall be added by 2050 to meet the offshore wind targets of the European countries, according to a ENTSO-E’s TYNDP report published in January 2024.
For decades, experts have discussed interconnections. However, two crucial factors are now driving their escalating importance: the increasing availability of renewables and the vulnerability of today’s network to climate change.
Grid interconnection—Boosting power reliability and stability, and reducing the reliance on fossil fuels
Put simply, an interconnection links a network of grids together at a synchronized frequency. This enables the transfer of surplus energy from areas with excess power to those with higher demand than they can meet locally. Harnessing electricity from a regional grid allows the local network to reduce the risks of power outages or failures, thereby boosting power reliability and stability.
In addition, interconnection links islands and continents to sources where renewable energy generation is more plentiful, thus progressively diminishing reliance on fossil fuels. Examples include the interconnection between Crete to Greece, Mallorca to Spain and Tasmania to Australia. This enables the development of renewable energy sources on these islands, freeing them from dependence on polluting power generation.
Here are five innovations that will make electrical transmission reach new heights.
Interconnections globally are instrumental in ensuring the viability of sustainable energy and reducing the reliance on fossil fuels. Achieving this requires a cutting-edge mindset in designing, manufacturing, and installing deep-sea cables that can transmit increasingly higher energy levels and that can realize interconnexions in previously impossible areas.
Moreover, innovation in electrical transmission is unquestionably linked to unerring monitoring as well as highly sustainable design.
From the engineering, manufacturing, construction, and installation of HVDC cables for connection systems, to the world’s first electrical Type Test with 320 kV HVDC cable termination using GE’s g³ gas to considerably lessen global warming potential, by way of the increasing amount of recycled metals used in cables: Nexans is at the forefront of these innovations.
In the coming weeks, we invite you to deep dive into these innovations that will revolutionize the electrical transmission industry.
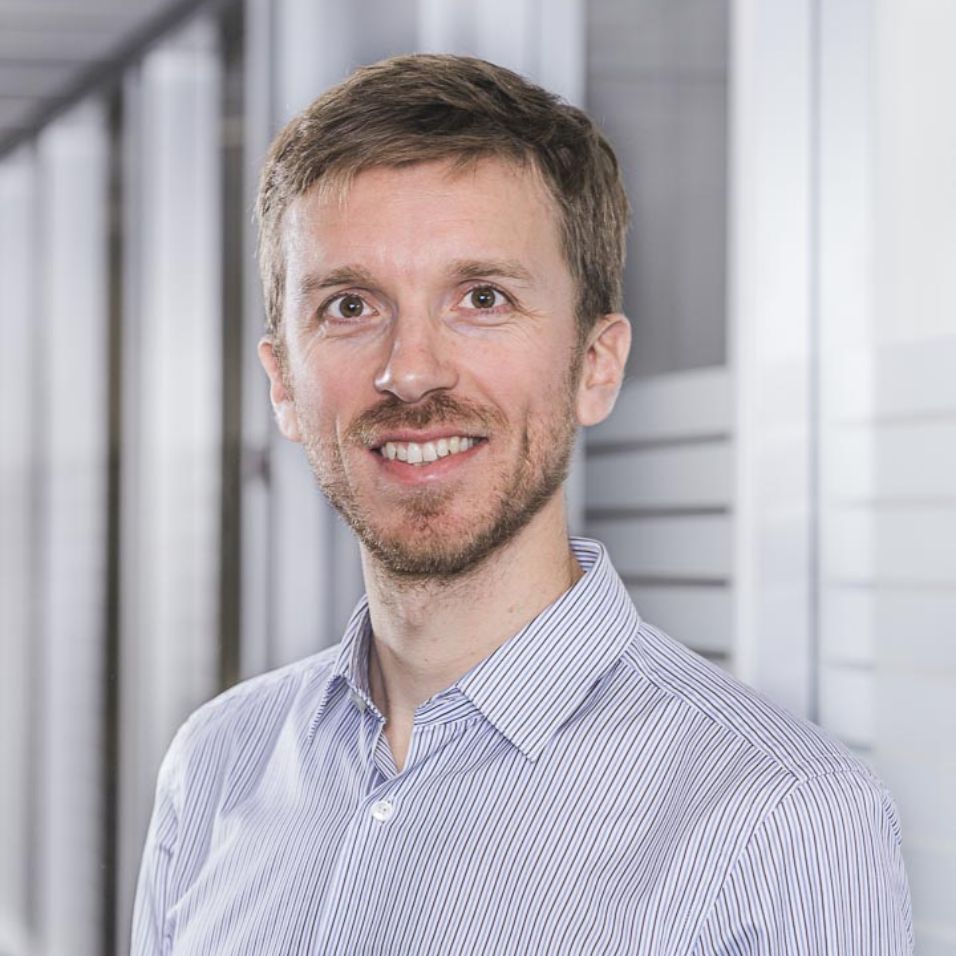
Author
Maxime Toulotte is the Markets & New Solutions Director of Generation & Transmission Business Group in Nexans, where he has the responsibility to develop and maintain relations with technical and engineering departments of clients and partners for subsea high voltage cables.
Maxime has held several positions as Sales & Tender Manager and Lead Engineer for high voltage submarine cable system projects.
Maxime holds a Master’s degree in Electrical Engineering from the Grenoble Institute of Technology, France.
The race to net zero is on, and to cross the finish line by 2050 industry needs to shed the burden of fossil fuels. But which energy sources have the power to replace them?
Although electricity is the undisputed front-runner when it comes to cleaner energy alternatives, electrification falls short in parts of the world that are isolated or lack solid electrical infrastructure. And this is without mentioning all the “hard-to-abate” sectors such as steel industry or intensive mobilities.
That’s where hydrogen steps in. The gas is already used as a chemical reagent in industries such as oil refining and agrochemicals, to the extent of 90Mt a year. And now a boom is on the cards, with demand predicted to increase by a factor of 4 to 6 by 2050. Production from water electrolysis would then account for over a quarter of the global power demand!
Decarbonizing hydrogen
But just how virtuous is hydrogen? Its production processes vary wildly in their environmental impact, leading to the informal and sometimes bewildering hydrogen rainbow classification system. The vast majority of hydrogen today comes from fossil fuels via high temperature steam reforming of methane, with 10kg of CO2 emitted for every kilogram of H2. This type of production is responsible for 2-3% of global CO2 emissions, on a par with air-travel!
Making hydrogen is also possible using electrolysis. This process, that splits water molecules into oxygen and hydrogen, is energy-intensive – 50-60 kWh generates 1kg of hydrogen. But when the electrolyzers are connected to renewable energy sources, very low-carbon hydrogen can be achieved.
However, its low density at room temperature means it must be compressed at high pressures – up to 700 bar – or cooled to a very low temperature – -253°C (20K) – to turn it into a liquid that can be transported and stored.
Furthermore, the carbon intensity of hydrogen produced by water electrolysis depends on the energy mix of the electricity source. In some countries with lots of coal power plants, the carbon footprint of electrolysis process could be more detrimental than steam methane reforming.
High-pressure challenges
New applications for hydrogen are springing up in the fields of energy and mobility. But to ensure the boom doesn’t run out of gas, big changes must be made over the whole lifecycle.
This starts with production. For hydrogen to truly contribute to a net zero emission world, the energy used for the electrolysis must come from renewable sources such as onshore or offshore wind and solar farms which Nexans already connects. This will have a direct impact on hydrogen’s price tag, which will then be driven by the costs of electricity and capital investment in farms and electrolyzer units.
Once it has been produced, all this hydrogen still has to reach the end user, and the right storage and transportation solutions could mean the difference between success and failure. Just one kilogram of hydrogen takes up 12m³ at atmospheric pressure, and very high pressures (up to 700 bar) are needed to bring this volume down to manageable levels.
The solution? Liquefy hydrogen. This has been a practice in aerospace for decades, and new applications for liquefied hydrogen (LH2) are emerging, such as:
- Overseas transportation of energy between production and consumption places. The Hystra project – producing hydrogen in Australia and shipping it by cargo to Japan – was a world first, enabled by Nexans high-flexibility cryogenic transfer lines. Projects aiming at deploying the infrastructures for maritime transportation of LH2 are now starting in key maritime ports to prepare the forthcoming worldwide trade of LH2.
- Aeronautics. Airbus is aiming to fly the first commercial plane fueled with LH2 in 2035. This will mean a complete change of airport infrastructures to supply hydrogen, electricity and sustainable aviation fuels, in places where safety and floor space are major stakes.
Innovation at every stage of the game
Nexans is contributing new technology and business solutions all the way down the hydrogen value chain.
- On the production side, we provide solutions for optimizing the operating and capital expenses of producing renewable energy. Applied to electrolyzing units, our unique know-how on grid design could help achieving optimized hydrogen production facilities
- On the storage and distribution side, Nexans has long been a pioneer in supply infrastructures for cryogenic fluids. Our vacuum-insulated flexible transfer lines offer easy-to-install, safe and reliable solutions for tank-to-tank transfer of LH2. Their “plug-and-play” installation is as easy as laying a power cable and beats conventional rigid piping systems when it comes to speed of implementation. We recently equipped the world first loading systems for ship-to-shore transfer of LH2 in Kobe, Japan, with long length, high flexibility cryogenic transfer lines capable of high flow rates, numerous bending cycles and minimal boil-off.
The future is hybrid
If smartly combined, electrification and hydrogen will team up to contribute to more efficient low-carbon energy supplies. Pushing forward the complementarity between the two energy vectors, we are currently developing new concepts of hybrid lines able to vehiculate both hydrogen and electricity in the same system, including:
- Subsea umbilical systems to transfer hydrogen, data and electricity between offshore production units, such as wind farms or energy islands, and land;
- Superconducting systems combining LH2 transfer and superconductivity for hybrid energy highways that can transmit impressive amounts of power over long distances and help modernize power grids.
Ultimately the transition to net zero will require a shrewd combination of many interlocking energy sources and technologies. Together with electrification, Nexans is empowering hydrogen to become a safe, effective, economically and environmentally viable contributor to the energy supply of tomorrow.
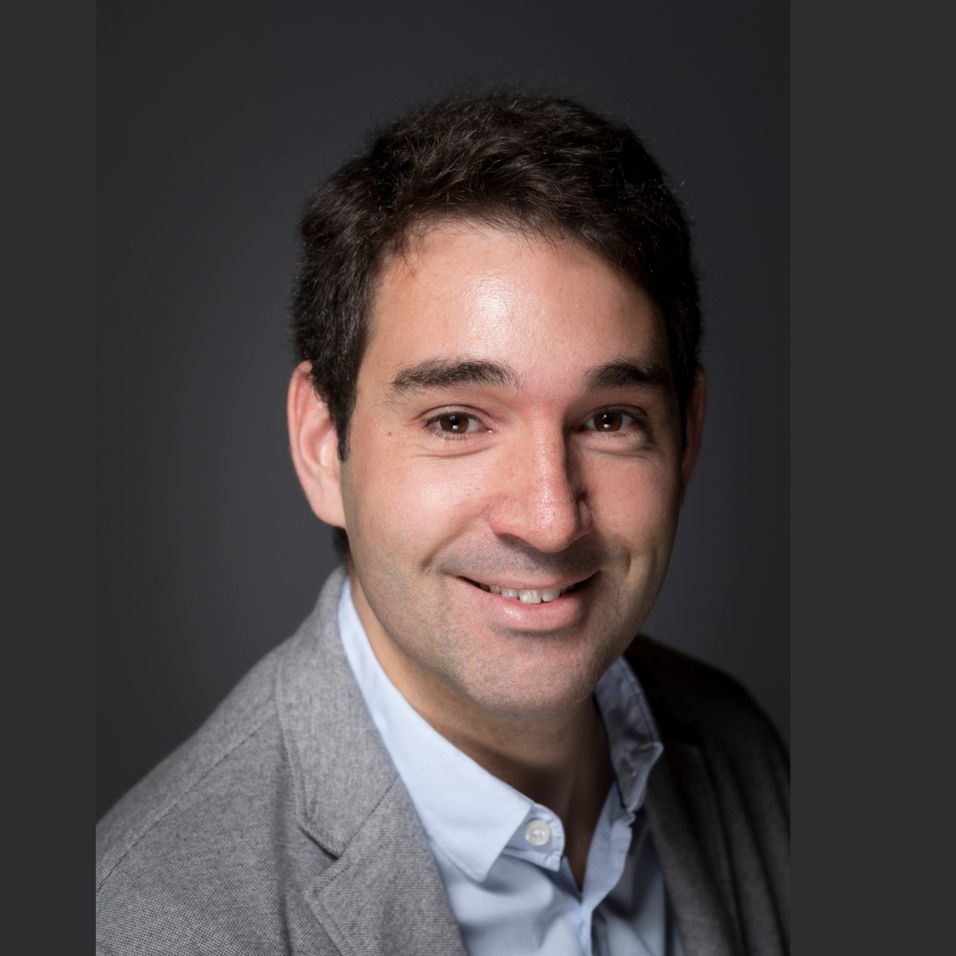
Author
Anthony Combessis is manager of the Hydrogen Techno-platform, at Nexans Innovation Services and Growth. He is in charge of identifying and developing innovations and new market opportunities for Nexans in the hydrogen ecosystem, with a special focus on cryogenics solutions. Anthony joined Nexans in 2011 as R&D project manager working on electrical vs. physical-chemical properties of polymers, instrumentation and nanocomposites. He holds a Ph.D. in polymer nanocomposites from Grenoble University, France.
Floating technology is a hot trend in the world of renewables. We examine the drivers and discover how Nexans is helping to turn the dream of floating offshore wind – and solar – into a reality.
Offshore wind generation has seen tremendous growth over the past decade. Global offshore capacity has now reached 35 GW – an almost nine-fold increase since 2011. An additional 235 GW of offshore capacity is expected by 2030, taking the global total to 270 GW.
Winds of change
Turbine technology has made huge strides since the first wind farms appeared in our oceans more than twenty years ago. Today’s turbines are bigger and more efficient than ever, with rotor diameters in excess of 200 metres and power ratings of 10 MW and more. These advances have played a critical part in driving down the cost of offshore wind.
Almost every offshore wind turbine in existence today depends on bottom-fixed foundations, which are a good solution in relatively shallow waters – those up to 60 metres deep. These foundations are steel and concrete footings that attach the turbine structure directly to the seabed.
The vast majority of oceans and seas have waters that exceed 60 metres in depth – and this is where the highest and most consistent winds are found. In Europe, for example, 80% of the wind resource occurs over waters with a depth of 60 metres or more. Conventional foundations are not cost effective in these situations. So there are large areas where wind resources are untapped.
New horizons for offshore wind
Floating wind turbines overcome the problem of providing foundations in deep water. Instead of being rooted to the seabed, turbines are mounted on a floating substructure that is tethered with mooring lines and anchors.
All of this is a game changer for offshore wind. Rather than being restricted to a depth of 60 metres, floating turbines can be deployed in waters up to 1000 metres deep – and potentially much more.
This has exciting potential to expand the geographical reach of offshore wind. The northern part of the North Sea basin is one example. The depth of waters here typically far exceeds 60 metres, putting them beyond the reach of conventional foundations.
Hywind Scotland in the UK – the world’s first floating wind farm – highlights what can be achieved. Sited about 30 km offshore in waters up to 120 metres deep, Hywind has been in service successfully since 2017. Hywind has the highest capacity factor for any wind farm in the UK: in 2020, it set a new UK record, achieving an average capacity factor of 57.1%. This compares to an offshore wind average in the UK of about 40%.
The technology behind floating wind is set to have an impact far beyond the North Sea, particularly in geographies where the sea gets very deep, very near the shore. Examples include the Mediterranean basin, the west coast of the United States, South Korea and Japan – all of which have huge offshore wind resources waiting to be tapped. Floating wind can also be deployed in shallow waters where seabed conditions prevent the use of conventional foundations.
Making floating wind a reality
Currently, floating wind accounts for just 0.1% of the offshore wind total. But that is set to change. Forecasts by the Global Wind Energy Council suggest that by 2030, floating wind could account for 6.1% of all new installations with an estimated 16.5 GW of new capacity added within the next ten years. Robust, cost-effective technologies hold the key to achieving this.
One of the big technical challenges with floating offshore wind is exporting the electricity they generate. There are three factors in play. First, cable links between wind farms and the shore are longer because turbines are typically sited further out to sea. Second, the power levels that must be handled are increasing as turbines grow in size. Third – and most importantly – dynamic cables are required. These must be capable of accommodating movements of the floater structure caused by currents, tides and wind. Resilience is critical.
Smarter dynamic cables
Nexans’ track record in high-voltage submarine cable systems and dynamic cables means the company is ideally placed to support the development of floating wind. Indeed, Nexans supplied dynamic cables for the Hywind Demo and Hywind Scotland floating wind projects. The company’s experience has deep roots: Nexans developed its first dynamic cable back in 1983.
Today, the innovation continues. The focus is now on developing HV dynamic cables that can handle more power and greater voltages than ever before. This new generation of cables will be lighter and more flexible than traditional subsea cables. They will also be smarter, thanks to the integration of optical fibre elements to provide real-time monitoring – providing critical information on various parameters of the cables and ensuring years of reliable operation.
Floating Wind Turbines: The skyscrapers of the sea
In this episode of What’s Watt, Frédéric Lesur and Maxime Toulotte present the ins and outs of floating wind turbines. How they are installed, how they generate energy, and how much energy they can produce from ocean winds. Get ready to face strong gusts, as you might be amazed by what you’ll see.
Floating offshore solar
Utility-scale floating solar power is one of the fastest-growing renewable technologies. Photovoltaic arrays are mounted on rafts anchored out in open water, with subsea cables to channel the power back to the land.
The most challenging aspect of the project from a cabling point of view is handling dynamic loading, caused by movement of the platform in response to wind, waves and tides. Nexans is utilising a three-core cable design of a type well-proven in offshore wind farm and fish farming installations. The 5 km cable is being manufactured at our Rognan plant in Norway.
The beauty of floating solar is that it dramatically expands the potential area available for siting solar arrays – without the need to acquire land. Growth in the floating solar sector is strong. Almost 10 GW of new floating capacity is expected to be deployed by 2025.
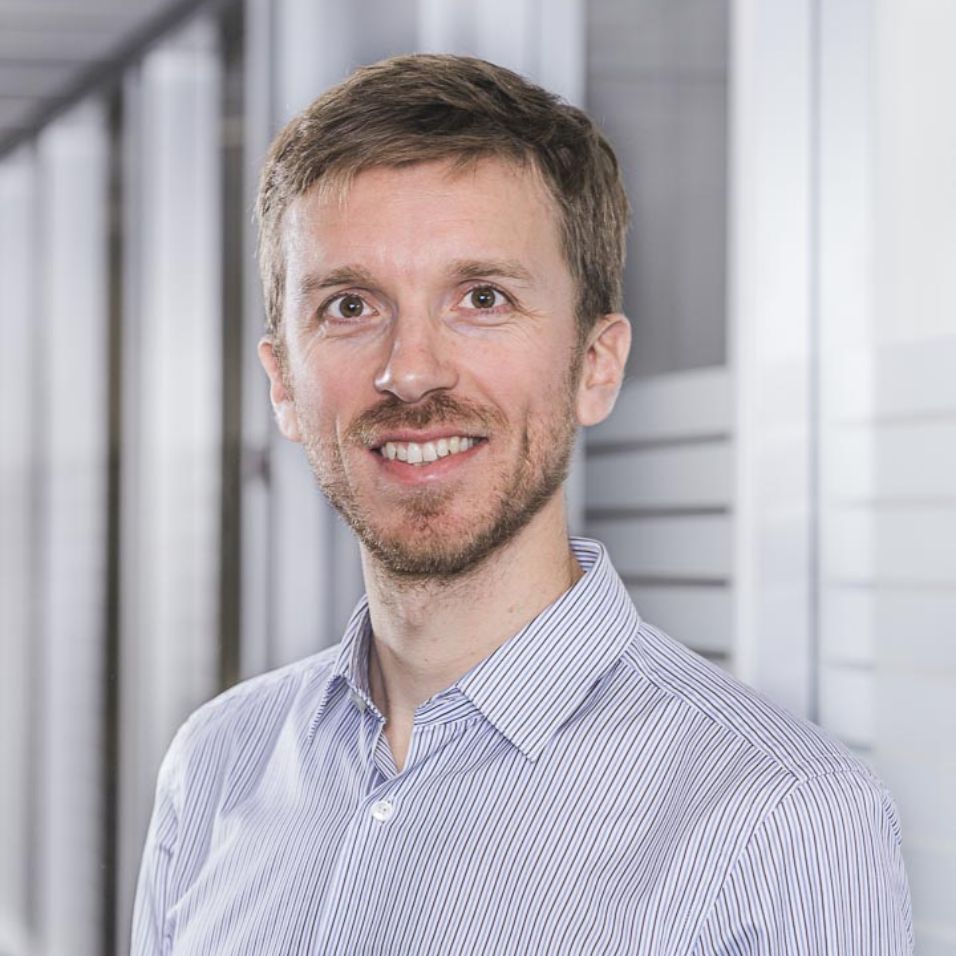
Author
Maxime Toulotte is the Head of Technical Marketing of Subsea and Land systems Business Group in Nexans, where he has the responsibility to develop and maintain relations with technical and engineering departments of clients and partners for subsea high voltage cables.
Maxime has held several positions as Sales & Tender Manager and Lead Engineer for high voltage submarine cable system projects.
Maxime holds a Master’s degree in Electrical Engineering from the Grenoble Institute of Technology, France.